Nature + Love project managers Focus Consultants are helping us consult with local residents of the Horniman, ahead of the site works due to take place starting later this year. The consultation is now complete.
You can find details of the Construction Environmental Management Plan below, including traffic and dust management plans.
We have indicated with * where information has been updated following the consultation. Some information has been deleted and this is indicated in the text below. Find a record of the draft Construction Environmental Management Plan and this page from the consultation.
Construction Environmental Management Plan
Focus Consultants has been appointed by the Horniman Museum and Gardens to identify best practice procedures for managing the construction activities associated with the following works:
- Contract 01: The refurbishment of The Natural History Gallery (NHG).
- Contract 02: The creation of a Sustainable Gardening Zone (SGZ) and associated
greenhouses with covered community space and an accessible toilet facility. - Contract 02: The creation of a Café and Ancillary Pavilion with toilet facilities and storage
and Nature Explorers Adventure Zone (NEAZ). - Contract 02: The Nature Trail (NT).
These procedures will ensure that the interests of neighbouring residents, businesses, general public and the visitors are given special attention by the Contractor during the duration of the works.
This report identifies how the critical activities will be approached, and specifically covers the environmental, public health and safety aspects of the proposed development.
The baseline for our analysis is the Lewisham Good Practice Guide Control of Pollution and Noise from Demolition and Construction Sites (GPG). We have viewed those requirements as the minimum standards to be achieved.
This document details the specific obligations on the Contractors when undertaking the works and the control measures to be employed for each environmental issue.
Nature of the Project/scope of works
The Natural History Gallery
- Careful removal of a few exhibition cases and upgrading of the remaining majority.
- Removal of existing ventilation, heating plant and equipment, replacing current ventilation with high level ventilation duct runs, and the creation of low-profile discreet ventilation louvre on underside of beam.
- Renovation of existing timber window and incorporation of new bespoke ventilation louvre.
- New handrail extension and associated structural support to first floor balustrade.
- Refurbishment, repair, and redecoration of all surface finishes.
- Removal of all roof coverings and reinstating with a lightweight insulated system, including the removal, renovation and re-installing the existing lanterns.
- The lowering of the external ground level along the external wall to be at least 150mm lower than any DPC that might be present.
Sustainable Gardening Zone
Provide propagation facilities that are modern and fit for purpose – automatic venting and heating using either a sustainable biomass boiler or air source heat pump and rain harvesting technology.
- The removal of existing poly tunnels and glasshouses and replacing with one single glasshouse freeing up more room for an uncovered hard standing area for plants.
- A glasshouse with water and heating, to be maintained with different climatic conditions when required including a potting area where staff can pot-on plants, store tools and materials safely. It can also be used to overwinter bulbs and tubers.
- Construction outdoor learning area focusing on sustainable gardening techniques. This covered space must also be used for community activities, with an accessible toilet and washing area.
- Major landscaping works to incorporate viewing area, improve accessibility to the South Downs, improve the horticultural offer, provide a community growing area, create winter plant interest using coloured stems, winter flowers, structural evergreen shrubs and trees and winter bulb display and the community growing area.
- Improving the water supply system. Only having one water point outside the zone, it is necessary to have at least two water points in different locations within the area. Capture rainwater from the roof of at least one of the buildings in the zone.
Nature Explorers Adventure Zone
- The construction of a cafe within the footprint of the Old Boating Pond to provide a food and drink offering that will only be open during daylight hours, with outside in-situ seating that will not be required to be stored away every evening.
- There will also be picnic tables around the café and the play space that families can use to eat at with bark/ wood chippings/Breedon gravel underneath.
- The existing path will be upgraded to enable vehicles to reach the café for deliveries and maintenance.
- There will also be an Ancillary Block to provide toilet and baby change facilities.
- Major landscaping to provide a new Nature Explorers Adventure Zone.
The Nature Trail
- Construction of new access from the gardens across the “Night Walk” to a new accessible ramped access to the Nature Trail. It should be noted that the Night Walk is a public footpath outside the curtilage of the Horniman Gardens.
- Construction of retaining walls.
- Changes to the route of the pathway, localised path widening.
- Additional bench seating and interpretation.
- Erection of a new storage shed.
Methodology for New Construction
This section identifies the specific methodology that we have identified for the whole project and each specific zone. We anticipate that the works within these zones will be carried out concurrently:
- Enabling and lead-in works
- Site Establishments
- Natural History Gallery (NHG)
- Sustainable Gardening Zone (SGZ)
- Nature Explorers Adventure Zone (NEAZ)
- The Nature Trail (NT)
Works are expected to start in Summer/Autumn* 2024 with a total duration of 18-24 months.
Enabling/Lead-in Works
The following schedules the activities to be carried out by the Main Contractor(s) to ensure works can be undertaken efficiently. Certain elements of these works will require third party approvals and should be prepared in sufficient time to avoid any delays to programme.
Production of a Site Environmental Management Plan.*- Mobilisation of selected sub-contractors.
- Production of a project Health and Safety Plan and risk assessments.
- Formulation of Site waste management plans and environmental plans.
- Production of project specific construction phase method statements for each individual area.
- Production of detailed works programmes and sequencing for each individual area.
- Surveys of existing services and structures to confirm methodology and load capabilities sequencing for each individual area.
- Highways condition surveys to be carried out prior to commencement on site.
- Building fabric condition surveys of areas adjoining the SGZ are to be carried out prior to commencement on site.
- Services investigations/surveys for decommissioning purposes.
- CCTV surveys of existing drainage.
- Hazmat and asbestos demolition and refurbishment (R&D) surveys, testing and ASB5 notifications to the HSE.
- Lewisham licence applications and approvals for hoardings and scaffolding.
- Baseline movement monitoring to areas adjoining the NHG.
- Baseline environmental monitoring.
- Neighbour liaison before the commencement on site to explain the nature of works and methods of communication with the contractor.
- Temporary works design.
- Take over liaison with UKPN regarding upgrade to power supply and build of cabinet.
Site Establishment, Security Management and Logistics
Site establishment can occur concurrently or prior to the enabling works. This activity can only begin when full possession of site areas has been given. The following activities will comprise the site establishment programme:
- Securing the external boundaries of each individual project area as appropriate. Establishing the internal demise within the NHG, isolating the site and the occupied parts of the building with fire rated and secure partition walls.
- Erection of a scaffold temporary roof over roof of the NHG.
- Establishing the vehicle and pedestrian access to the works. Routing of temporary vehicular to the NEAZ to be agreed and constructed. All routes are to be controlled by fully trained gatemen and traffic marshals.
- Installation of site temporary electrics, lighting, water and fire alarms.
- Establishment of a 24/7 site security provision with CCTV perimeter support to ensure that all individual sites are protected against unauthorised or unlawful entry and potential theft from site. This will be supported by the Horniman 24/7 Security Officer.
- All existing services and systems within the NHG and SGZ are to be traced and isolated. Diversions of existing utilities, if required, will be carried out at an appropriate point in liaison with the statutory service providers.
- Site offices will be established on the first floor of the NHG for Contract 1 (NHG).
- Site offices for Contract 2 will be located as per Appendix A.
- Initial site welfare arrangements will be established in appropriate locations for all individual sites.
- Emergency routes on site specified and clearly signposted.
- Early site investigations for location and safeguarding of historic fabric.
- Instigation of a full Refurbishment and Demolition Asbestos Survey.
- Structural investigation surveys and trial holes.
Natural History Gallery
The NHG work will be let as an individual contract and treated as an individual site as it is easily defined with a distinct separate site boundary, site access, and space for separate welfare facilities. The following activities will comprise the works:
- A refurbishment and demolition (R&D) asbestos survey will be undertaken after vacant possession.
- Live services to be isolated. An advance desk top study of all existing services will have been carried out in the pre-construction phase.
- All operatives and site staff will be directed to remain vigilant regarding the heritage features and structural integrity of the building during the soft stripping works, which include the removal of existing ventilation and heating plant and equipment.
- The works will be carried out using hand tools/hand-held plant, with materials removed via the rear entrance point as bagged material or in wheelie bins. The material will then be deposited into skips within the site compound in the rear car park area for removal from site.
- Regularly removing the accumulated debris will minimise the potential fire risk that loose combustible material poses.
- A scaffold temporary roof is under consideration to allow roof works to be undertaken without risk of damage to existing building fabric.
- Materials will be removed and delivered to the roof via a scaffold hoist system.
- Plantrooms and core distribution will take early priority, followed by distribution of services across floors.
- Refurbishment, repair, and redecoration of the internal spaces will be undertaken as soon as the new works are complete, and the area is watertight.
Sustainable Gardening Zone (SGZ)
The SGZ work will be let as a joint contract with the NEAZ and NT. The following activities will comprise the works:
- Refurbishment and demolition asbestos surveys will be undertaken on the two greenhouses, the boiler shed and the polytunnel prior to demolition.
- Live services to be isolated. An advance desk top study of all existing services will have been carried out in the pre-construction phase.
- All operatives and site staff will be directed to remain vigilant regarding the existing flora and fauna that will remain within the site boundary, this will include, but not be limited to tree root, soil and grass protection.
- All existing structures to be demolished and any foundations grubbed up. The materials arising will then be deposited into skips within the site boundary for removal from site.
- The substructure works for the buildings and the hard and soft landscaping will be carried out using mechanical plant and equipment, with materials arising deposited into skips within the site boundary for removal from site.
- The construction of the new glasshouse and associated hard and soft landscaping will be carried out using hand tools, hand-held plant, mechanical plant and equipment. Due to the proximity of visitor to the garden, use of hand-held tools will ensure noise and vibration are kept to the minimum.
- Planting is preferable to be carried out in the relevant planting seasons.
- All works are to be carried out with reference to and in line with the Arboricultural Impact Assessment.
Nature Explorers Adventure Zone (NEAZ)
The NEAZ work will be let as a joint contract with the SGZ and NT. The following activities will comprise the works:
- Live services to be isolated. An advance desktop study of all existing services will be carried out in the pre-construction phase.
- All operatives and site staff will be directed to remain vigilant regarding the existing flora and fauna that will remain within the site boundary.
- All existing structure to be demolished and any foundations grubbed up. The materials arising will then be deposited into skips within site boundary for removal from site.
- The substructure works for the buildings, hard and soft landscaping will be carried out using mechanical plant and equipment, with materials arising deposited into skips within site boundary for removal from site. Nature + Love Project: Construction Environmental Management Plan R2786 CEMP 240212 10 Focus Consultants 2010 LLP
- The construction of the new Kindercafe, Ancillary Block, and associated hard and soft landscaping will be carried out using hand tools, hand-held plant, mechanical plant and equipment. Due to the proximity of visitor to the garden, use of hand-held tools will ensure noise and vibration are kept to the minimum.
- Planting is preferable to be carried out in the relevant planting seasons.
- All works are to be carried out with reference to and in line with the Arboricultural Impact Assessment.
The Nature Trail (NT)
The work NT will be let as a joint contract with the SGZ and NEAZ. The following activities will comprise the works:
- Live services to be isolated. An advance desk top study of all existing services will be carried out in the pre-construction phase.
- All operatives and site staff will be directed to remain vigilant regarding the existing flora and fauna that will remain within the site boundary.
- The hard and soft landscaping will be carried out using mechanical plant and equipment, with materials arising deposited into skips within site boundary for removal from site.
- The work to the trail will be carried out prior to the construction of the NT gate, bridge and access ramp.
- Planting is preferable to be carried out in the relevant planting seasons.
- All works are to be carried out with reference to and in line with the Arboricultural Impact Assessment.
The Construction Site
This section sets out procedures that should be implemented during site operations relating to site management practices
Working Hours
- Lewisham’s GPG states Site Working Hours will be:
- Monday to Friday: 8am – 6pm
- Saturday: 8am to 1pm but not significantly noisy work which will impact on neighbouring properties.*
- Sunday and Bank Holidays: No work where noise audible at site boundary.
- The Horniman’s Gardens are open to the public as follows:
- Monday to Saturday gates open at 7:15 am.
- Sunday and Bank Holidays gates open at 8:00 am
- The Gardens close at the following times in 2023:
- Monday 5 February – Sunday 3 March: 5.30pm
- Monday 4 March – Sunday 31 March: 6.30pm (British Summer Time starts)
- Monday 1 April – Sunday 5 May: 7.30pm
- Monday 6 May – Sunday 25 August: 8.30pm –
- Monday 26 August – Sunday 29 September: 7.30pm
- Monday 30 September – Saturday 26 October: 6.30pm (British Summer Time ends)
- Sunday 27 October – Sunday 2 February 2024: 4.20pm
Public opening hours are expected to be similar in 2024.
All vehicles and plant arriving at and leaving the site should comply with the same restrictions on hours. The main contractor should be held responsible for ensuring these instructions are given to all drivers, including those delivering site materials.
Any deviation from these hours will require prior approval from the Lewisham Environmental Protection Team.
Good Housekeeping
The Contractor will follow a ‘good housekeeping’ policy at all times. This will include, but not necessarily be limited to the following. The Contractor will:
- Ensure considerate site behaviour of the Contractor’s staff.
- Ensure the noise from lorry reversing alarms are kept to minimum levels.
- Prohibit open fires.
- Ensure that appropriate provisions for dust control and road cleanliness are implemented, to both the adjoining residential roads on the Horniman’s Gardens estate roads.
- Remove rubbish at frequent intervals, leaving the site clean and tidy.
- Frequently inspect, repair and re-paint as necessary all site hoardings to comply with the conditions of the Lewisham’s GPG section 9.11 and any relevant Licence. – all flyposting and graffiti are to be removed as soon as reasonably practicable and within 24 hours of its appearance.
- Maintain toilet facilities and other welfare facilities for its staff.
- Remove food waste.
- Prevent vermin and other infestations; and undertake all loading and unloading of vehicles as identified on the logistics drawings.
Community Liaison
Lewisham Council considers that liaison with local residents who may be affected by construction works is essential and this is set out with GPG section 2.2 Community Liaison and Complaint Resolution. The Contractor will arrange a public meeting to provide information about the further coming works prior to starting on site. This will include information about traffic management, pedestrian movement, waste management, dust management etc. We are not anticipating any flood lighting or drive piling to be required but if they are, the Contractor should notify local residents in advance of these items being
carried out.
If flood lighting is required it must be set up so as not to be directed into the windows of residential properties.*
Communication to local residents should include publicity, including the name and telephone number of a main contact which should also be displayed on the site hoardings. This contact person should be able to give further information to the caller and deal with any complaints or emergencies that may arise at any time. A copy of the letter to be sent to residents along with the planned distribution list should be included with the return form in Appendix 1 of the GPG and sent to Lewisham’s Environmental Protection Team at least 28 days before the start of works.
Complaints should be reported to Lewisham’s Environmental Protection Team within 24 hours by telephone and/or email, investigated and where appropriate measurements taken and where necessary mitigation methods implemented, or work practices modified.
The results of the investigation, along with details of any mitigation methods implemented or work practice that has been modified and how complainants have been kept informed should also be sent to Lewisham’s Environmental Protection Team as soon as possible.
All site staff are to be regularly briefed regarding the complaint procedure.
Security
- The Contractor is to ensure that each individual site, the site compound and any satellite storage compounds are secure and prevent unauthorised entry to all areas.
- Site gates will be closed and locked when there is no site presence. Alarms will incorporate an appropriate cut-out period.
- Access and egress will be via manned security gates.
Hoardings, Site Layout and Facilities
- Each individual site will be completely secure to deter public access.
- The proposed hoarding line and gates, all of which will be in accordance with the GPG, are shown on the enclosed plans.
- Site welfare arrangements are expected to be located within easy reach of each individual site area.
Emergency Planning and Response
The Contractor will develop a plan for emergencies to incorporate:
- Site specific risk assessment.
- Ensure appropriate site induction for all contractor teams to include information around pollution control and reporting procedure.
- Emergency procedures including emergency pollution control to enable a quick response.
- Emergency phone numbers and the method of notifying Lewisham and statutory authorities. Contact numbers for the key staff of the Contractor will also be included.
- The Contractor will display a ‘contact board’ on the hoarding identifying key personnel with contact addresses and telephone numbers, so that members of the public know who to contact in the event of a report or query.
- London Fire and Emergency Planning Authority (LFEPA) requirements for the provision of site access points.
- Site Fire plan and management controls to prevent fires.
- A plan to reduce fire risk and potential fire load during construction, operation and subsequently during maintenance or repair. The project will comply with any third-party requirements as may be appropriate at specific sites.
- A plan to respond to a pollution incident on site, including details of reporting to client and relevant authorities
Hoists
- To deliver materials to the roof of NHG will be via an external hoist positioned on a pavement gantry.
- A small mobile hydraulic crane is expected to be in operation at the site of the Boating Pond (café and play area).
Considerate Constructors Scheme
- The site is to be registered with the ‘Considerate Constructors Scheme’ and the ‘Freight Operator Recognition Scheme’.
- These schemes ensures that contractors carry out their operations in a safe and considerate manner with due regard to neighbours, passing pedestrians and road users.
- Traffic Marshalls/Banksmen will monitor incoming vehicles and will marshal construction vehicles and materials as they move around the site.
- Safe pedestrian routes will be clearly marked, and construction vehicles and materials will be escorted to avoid obstructing these routes.
- The local community will be engaged with and access to information relating to the construction will be made available.
- Carbon will be minimised throughout the supply chain.
- The Code of Considerate Practice will be adhered to: The Code of Considerate Practice – Considerate Constructors Scheme (ccscheme.org.uk)
Site Logistics
The Traffic Management Plan (TMP) is included at Appendix C of this document. Please note that as there will be two contractors on site at the same time, this TMP will apply to each of them. The Natural History Gallery Contractor will take overall responsibility for managing and coordinating site deliveries and providing related facilities such as vehicle wash.*
Lewisham recommends that a Construction Logistics Plan (CLP) is submitted for their review, this is also an essential document that will be vital to the success of the project.*
The CLP provides the key logistics strategy for the project and ensures that the products and materials arrive on site at the time and in the quantities that are required.*
Feilden Fowles’ draft drawings NLP-FF-00-XX-DR-A-00119 – Proposed Construction Management Site Plan illustrate the proposed overall logistics plan for the site (see below in Appendix A), which incorporates the following key features:
All construction and delivery vehicles with a gross weight of 3.5 tonnes or more (Heavy Good Vehicles) shall be required to enter and leave the site via the London Road (A205) main entrance gate. Light good vehicles may use either the London Road gate or Horniman Drive gate, subject to the restrictions set out in this plan, concerning hours of use and adherence to the approved route.
All large deliveries via London Road between 6am – 9am and 2pm – 3pm.
Smaller deliveries via Horniman Drive between 9:30am – 11am.
- All construction and delivery vehicles shall be required to enter and leave the site via the London Road (A205) main entrance gate.*
- All deliveries in relation to the project via London Road between 6:00am – 9:00am and 2:00pm – 3:00pm.*
- Occasional overnight deliveries may be required to avoid visitors and heavy traffic, to be discussed and agreed with the Horniman and Local Authority. Overnight deliveries would have to be made via the London Road entrance.
- Vehicle access to Michael Horniman Building to be retained throughout.
- Grass bank area behind the Michael Horniman Building’s (MHB) North Hall fire exit is earmarked for Contractor’s compound for Contract 1.
- Various areas are identified as Contractor’s compound for Contract 2.
- Location of temporary footpath for Horniman and Contractor staff identified.
- Location of MHB existing fire escape route identified and must be retained throughout.
- Tree Route Protection areas will be reviewed and, where necessary and possible, the widening of paths will be considered to ensure ecology is protected.
- Access for event hires in the Conservatory Building are to be maintained, including areas for temporary marquees and deliveries.
- Blue Badge Parking Spaces will be maintained, and the Contractor will ensure access to the three spaces is not hindered by works on site.
The Contractor is to take onboard the draft Proposed Construction Management Site Plan and all other relevant information any fully develop the CLP.
Traffic Management
This section highlights the measures the Contractor may adopt to avoid nuisance to the public that may arise from increases in traffic flows.
All construction and delivery vehicles related to the construction works for Nature + Love shall be required to enter and leave the site via the London Road (A205) main entrance gate. There are expected to be up to twenty deliveries per week in relation to the construction works (approx. 10 per Contract).*
All construction and delivery vehicles with a gross weight of 3.5 tonnes or more (Heavy Good Vehicles) shall be required to enter and leave the site via the London Road (A205) main entrance gate. Light good vehicles may use either the London Road gate or Horniman Drive gate, subject to the restrictions set out in this plan, concerning hours of use and adherence to the approved route.
There are expected to be up to twenty deliveries per week in relation to the construction works.
The GPG states that all vehicles and plant arriving at and leaving the site should comply with the same restrictions on hours. The main contractor will be held responsible for ensuring these instructions are given to all drivers, including those delivering site materials and coordinating between different suppliers when there are multiple deliveries in the same time period. There will be wheel/ chassis wash facilities at the entrance to the site suitable for the size and type of vehicles.
The Natural History Gallery Contractor will be responsible for the provision of these facilities along with Traffic Marshalls and overall management of the deliveries.*
All smaller vehicles which are making deliveries via Horniman Gardens will be restricted to use A205, Honor Oak Road and Westwood Park to access Horniman Gardens, to stop unsuitable traffic using residential roads in the area.
Prior to commencement of works, a meeting will be held with the Horniman site management team (including Security and Estates) to agree delivery arrangements. This will ensure priority access is given to the Horniman deliveries (estimates of 10 per day).
Arrangements for delivery, unloading, disposal of waste etc. requires careful planning and programming, deliveries must be arranged with the Site Manager or their nominee to enable co-ordination. Traffic Marshalls will be provided to control site deliveries for both arrival and departure of all delivery vehicles, plant and materials being moved around site. Strict controls will be enforced; Contractors must give 48 hrs /2 working days’ notice of deliveries and/or collections. Vehicles arriving out of sequence will be turned away. Special loads will possibly require several weeks’ notice pending Horniman and Local Authority approvals.
The Contractor will endeavour to ensure that all heavy vehicle traffic is limited to times outside of rush hour, Monday to Friday. Construction vehicle movement will also be carefully planned and coordinated to avoid the AM and PM school drop off and collections. This will reduce congestion and safeguard pedestrians.
Safety of cyclists is of paramount importance and all vehicles entering and exiting the site will fully comply with CLOCS, the requirement for vehicular safety equipment. Deliveries will abide by London standards recommended by the Construction Industry Cycling commissioning manifesto. (To note, as per the Horniman policy, no cycling is permitted around the grounds and cyclists must dismount and use the cycle parking provided.)
As the London Road entrance is also used by some pedestrians, there will be pedestrian management at this point and Traffic Marshalls will direct any vehicles or materials moving through the Gardens. A traffic management system will be put in place to ensure the safe turning of vehicles into and out of the London Road entrance.
There may be specific need to work outside of the hours set out in 4.1 to manage certain noisy works and deliveries to limit impact on the calendar of public events. In these circumstances the contractor will liaise with all parties, including Lewisham and TfL as applicable.
Indicative types of on-road vehicles arriving and departing the site are as follows:
Via London Road:
9.11m (6) wheeled rigid “muck-away lorry
8.73m (6) wheeled rigid ready mix concrete lorry
7.90m (4) wheeled skip lorry
Via Horniman Drive:
6.65m (4) wheeled rigid small Flat bed with Hiab delivery lorry
5.2m (4) wheeled general delivery van
- 9.11m (6) wheeled rigid “muck-away” lorry
- 8.73m (6) wheeled rigid ready mix concrete lorry
- 7.90m (4) wheeled skip lorry
- 6.65m (4) wheeled rigid small Flat bed with Hiab delivery lorry
- 5.2 m (4) wheeled general delivery van.*
All on-road vehicles will comply with the Ultra Low Emission Zone (ULEZ) vehicle emission standards as a minimum. Evidence that contractors and suppliers have been contacted and their responses to the applicant in respect to the use of ULEZ compliant vehicle a ULEZ vehicle compliance form for the construction works will be issued to the London Borough of Lewisham Council monthly by e-mail. The use of Ultra-Low Emission Vehicles (ULEV) (e.g., Electric, Hybrid (Electric-Petrol) where possible will be encouraged at the procurement stage of the tender for these services.
The Contractor will actively work with suppliers that can provide electric or hybrid vehicles. Subcontractors will be required to comply with the emission hierarchy where practicable. A software platform will be used to monitor the carbon footprint of deliveries, tracking the start, finish location and means of transportation. The ULEZ vehicle emissions compliance will be monitored monthly log sheet.
Indicative Non-Road mobile machinery (NRMM) types for site use as follows:
- Telehandler-Material distribution
- Mini Excavator-Earthworks
- Dumper-Earthworks
- Spider crane-Lifting
All deliveries to site will be undertaken with full regard paid to:
- Reduction and control of plant movements
- All vehicles to be directed by a competent person
- Pedestrian and vehicle directional signage – suitable barriers will be erected to prevent pedestrian crossing the site entrances when deliveries are taking place.
- Mobile plant will only be operated by a competent person with a bank’s person in attendance to any movements
All non-road mobile machinery (NRMM) will comply with Stage IV Emission Standards (or the latest standard if the GLA requirements change) as a minimum if equal to or over 37kW. Where compliance with Stage IV requirements is not achievable or practical, an exemption will be sought from the GLA prior to arrival of the equipment on site.
There is no parking available on site for contractor vehicles and parking in local streets is very limited, all contractors and sub-contractors’ operatives should be encouraged to use public transport wherever possible.
Site Waste Management
The Contractor will carry out the works in such a way that, as far as is reasonably practicable, the amount of spoil and waste (including groundwater, production water and run-off) to be disposed of is minimised, and that any waste arising from the site is properly categorised and dealt with in accordance with the appropriate legislation and guidance. Opportunities for re-using or recycling construction or demolition waste should be explored and
implemented.
A formal and detailed Waste Management Plan will be prepared by both* Contractors*. The disposal of all waste or other materials removed from the Site will be in accordance with the requirements of the Environment Agency, Control of Pollution Act (COPA), 1974, Environment Act 1995, Special Waste Regulations 1996, Duty of Care Regulations 1991 and the Waste Management Regulations 2006.
Waste should be stored away from boundaries where possible, and carefully managed not to cause harm or nuisance to neighbouring properties.
This approach complies with the waste hierarchy whereby the intention is first to minimise, then to treat at source or compact and, finally, to dispose of off-site as necessary. All relevant Contractors will be required to investigate opportunities to minimise and reduce waste generation, such as:
- Agreements with material suppliers to reduce the amount of packaging or to participate in a packaging take-back scheme.
- Implementation of a ‘just-in-time’ material delivery system to avoid materials being stockpiled, which increases the risk of their damage and disposal as waste.
- Attention to material quantity requirements to avoid over-ordering and generation of waste materials.
- Re-use of materials wherever feasible (e.g. re-use of crushed concrete from demolition process for fill; re-use of excavated soil for landscaping; re-use of internal equipment and plant from existing buildings). Concrete will be taken off the site for crushing and re-use.
- The Government has set broad targets of the use of reclaimed aggregate, and in keeping with best practice, Contractors will be required to maximise the proportion of materials recycled.
- Segregation of waste at source where practical. Where on site waste segregation is not practical it will be segregated off site by the Contractor.
- Re-use and recycling of materials off-site where re-use on-site is not practical (e.g., through use of an off-site waste segregation facility and re-sale for direct re-use or reprocessing). Our expectations in this regard are shown below.
- Architectural salvage – 100% re-used – several architectural salvage companies in London
- Structural steel for re-use – 100% re-used – any complete sections salvaged during the demolition works will be retained by the Contractor for re use in temporary works or recycled as scrap metal.
- Metals – 100% recycled – Every effort will be made to recycle these materials on site with any surplus being taken to waste transfer station.
- Hardcore (brick/block/concrete etc.) – 100% recycled – Taken off-site to be crushed and reused
- Excavated material/clay etc. – 100% recycled – Clay – 100% processed for re-use as fill material (subject to analysis).
- Timber – up to 80% re-used. The amount re-used will depend on the material – we will attempt to salvage any re-useable timber for hoardings, battening, shuttering etc. for possible use on site with the balance being retained by the Contractor
- Glass (non-tempered, non-laminated and nonbomb proofing film etc.) – 100% recycled – Processing facility in Greenwich & Park Royal.
- Mixed waste – the amount recycled will depend on the material – An absolute minimum will remain for transport to landfill.
- Asbestos – 100% landfill – Taken to a licensed site.
Overall, the waste management for the site is likely to comprise of the following:
- Waste arising from stripping out, demolition and minor excavations will be removed from site by wheelie bin to waste lorries and taken to an off-site waste management centre for segregation and recycling.
- Packaging will be minimised and where possible removed from site on the same delivery vehicle that brought it to site.
- General waste will be removed from site by wheelie bin to a waste lorry daily. Waste material will not be allowed to be retained on site. Ideally the contractor will operate an evening back shift for removal of rubbish each day.
Noise and Vibration
The Horniman and the Contractor will agree a baseline for which the Contractor will monitor and control levels of noise and vibration from the site.
Lewisham’s GPG section 3 set out their requirements for the control of Noise and Vibration.
Noise control
The Contractor’s environmental team will undertake a noise assessment using noise predicting software which projects noise levels at adjoining properties based on the emissions made by specific plant. This noise assessment will be carried out in accordance with BS5228-1 2009 ‘Code of Practice for noise and vibration on construction and open sites and is above the requirements of the GPG.
This assessment allows the Contractor to select the most appropriate plant, methodology and controls to minimise disruptions of buildings at close proximity of the adjacent structures (sensitive receptors) and in particular live and occupied premises during the demolition and alteration phases.
Noise levels will be monitored by the Contractor during the course of the demolition and construction works. Lewisham shall be given access to all noise readings if required as soon as they become available.
Although the noise levels to be included in a formal agreement between the Contractor and Lewisham are the maximum to be allowed, at sensitive locations the Contractor will be requested to achieve, where practicable, noise levels lower than the specified limits.
Site operatives must be conscious of raised voices when arriving, leaving and whilst on site to minimize impact on local amenity.*
Noise Control Provisions – Screens and Scaffolds
The Site Manager will notify the Client of any planned noisy works in the regular logistics meeting.
Where hard demolition occurs inside the Natural History Gallery*, breaking out will be undertaken by handheld tools. Working hours will be managed to suit the operations of the Horniman and the working operations of neighbours as far as possible. This might mean undertaking noisy works between 8am and 10am, followed by a quiet period of clearing away.
Physical barriers will be deployed where possible to contain noisy operations within the working area as far as possible. Structural born noise will be monitored, and times of work managed to limit disruption to others.
Vibration Control
The Site Manager will notify the Client of any planned works that may result in vibration in the regular logistics meeting.
Vibration is a particular risk during structural breaking out in close proximity to heritage finishes. The measures taken to reduce the acoustics of these operations will also assist in mitigating the effects of vibration on the existing building and neighbours.
The Contractor will comply with the vibration levels established by agreement with Lewisham.
Equipment is to be selected giving consideration to noise and vibration. Where noise is unavoidable noise assessments are to be made and, if necessary, hearing protection zones established. Consideration will be given to the neighbours with consultations.
Operatives who are required to use vibrating equipment must be made aware of the health risks associated and their exposure must be monitored and recorded.
In areas where vibration is a risk to Museum objects, vibration sensors will be utilised to monitor vibration and alert the Contractor if maximum levels are exceeded so that works can ceased.
Works which may course high levels of vibration near residential properties e.g. construction of foundations for the café, should not take place on Saturday mornings but be restricted to Monday-Friday, 8am – 6pm.*
Air Quality and Dust Minimisation
The Contractor will, as far as reasonably practical, seek to control and limit emissions to the atmosphere in terms of gaseous and particulate pollutants from vehicles and plant used on site and dust from construction activities.
Lewisham’s GPG section 4 set out their requirements for the control of Dust and Air Pollution.
Throughout the project the Contractor will ensure the following:
- There is no burning of waste materials on site.
- There is an adequate water supply on the site.
- Disposal of run-off water from dust suppression activities and is in accordance with the appropriate legal requirements.
- A Dust Management Strategy will be implemented.
- All dust control equipment is maintained in good condition and record maintenance activities.
- Where creation of dust is unavoidable personnel must use appropriate RPE. N.B. RPE will often be required when wet cutting stone or concrete. Stringent control measures must eliminate, minimise nuisance factor to the general public in accordance with environmental requirements.
- Consideration must be given to the use of vacuum attachments to tools used in operations that will produce dust e.g. circular saw on insulation/plasterboard. The decision not to use such attachments must be justified within the risk assessment. Damping down is an alternative control method if dust capture/containment is not reasonable.
- Site hoarding, barriers and scaffolding are kept clean.
- Loading of material into lorries within designated loading areas.
- If necessary, clean public roads and access routes using wet sweeping methods.
- Vehicles held on site for any reason have exhausts positioned such that the risk of resuspension of ground dust is minimised.
- All vehicles carrying loose or potentially dusty material to or from the site are fully sheeted.
- Minimise the amount of waste material held on site.
- Sheet, seal or damp down unavoidable stockpiles and skips of excavated material held on site, where required.
- Avoid double handling of material wherever reasonably practicable.
- Ensure water suppression is used during demolition operations.
- Use enclosed rubble chutes and conveyors where reasonably practicable or use water to suppress dust emissions from such equipment.
- Sheet or otherwise enclose loaded bins and skips.
- Minimise drop heights from conveyors, loading shovels, hoppers and other loading or handling equipment and use fine water sprays on such equipment wherever appropriate.
- Use prefabrication of goods and materials to reduce the need for grinding, sawing and cutting on site wherever reasonably practicable.
- Only use cutting, grinding or sawing equipment fitted or in conjunction with suitable dust suppression techniques such as water sprays or local extraction.
- The engines of all vehicles and plant on site are not left running unnecessarily to prevent exhaust.
- Use low emission vehicles and plant fitted with catalysts, diesel particulate filters or similar devices.
- Use ultra-low sulphur fuels in plant and vehicles.
- That plant will be well maintained, with routine servicing of plant and vehicles. On site servicing and maintenance to be carried out where possible.
- That all project vehicles, including off-road vehicles, hold current MOT certificates where required.
- Carry out site inspections regularly to monitor compliance with dust control procedures set out above and record the results of the inspections, including nil returns, in the log book detailed.
- Increase the frequency of site inspections when activities with a high potential to produce dust are being carried out and during prolonged dry or windy conditions.
- Record any exceptional incidents causing dust episodes on or off the site and the action taken to resolve the situation in the log book detailed in above.
The Contractor will ensure that dust monitoring will be carried out during potential dust producing activities. The assessment will look at the dust raising potential of demolition and construction activities proximity to potential receptors and the duration of construction activities at each location.
Further information about this is provided in Appendix D.*
Protection of Historic Fabric
The Contractor will properly safeguard all buildings, structures, works, services or installations from harm, disturbance or deterioration during the construction period.
This will be achieved by providing the necessary support and protection that the existing fabric requires.
Prior to commencing any demolition and alterations works, the Contractor will prepare a schedule of buildings, structures and services within the zone of influence of the proposed works.
To comply with the above requirements, it will be necessary to ensure the following procedures are established:
- Existing fabric must be accurately surveyed and assessed to ensure that the proposed works are technically feasible.
- Works to be undertaken by suitably qualified specialist Contractors using skilled and experienced operatives.
- Careful monitoring of fabric as works proceeds.
- Ensure any retained structure is fully protected during the construction process to prevent environmental or accidental damage.
- Specialist Contractor to prepare detailed method statement for agreement with all third parties prior to works commencing.
- Submit permit to work procedure to be established between all interested parties.
Managing the Environmental Impact of Construction
This section sets out the requirements on the Contractor for managing the environmental impacts of constructing the development.
The Contractor must demonstrate in detail how the requirements of the GPG will be met.
The Contractor will need to demonstrate the management, monitoring, auditing and training procedures that are in place to ensure compliance with the GPG. The contractor will set out the specific roles and responsibilities of their personnel in managing, monitoring all of the works, including any sub-contractors.
The specific measures to be implemented by the Contractor will include:
- The Contractor will liaise with Lewisham’s Environmental Protection Team on a regular basis, agreeing routine arrangements for each site’s activities and ensuring compliance with the GPG.
- The Contractor will provide toolbox talks on environmental topics such as Tree Protection Zones, slow-worm Anguis fragilis, common lizard Zootoca vivipara etc.
- The Contractor will ensure any holes or openings are appropriately closed up at night to prevent harm to people or ecology.
- The Contractor will be responsible for establishing and maintaining contact with Lewisham and local residents, and keeping them informed of construction matters likely to affect them.
- This liaison will include the regular and frequent distribution of Newsletters and attendance at meetings at the request of Lewisham and or representatives of local residents’ groups.
- The Contractor will advise Lewisham within 24 hours of any incidents of non-compliance with the GPG and health and safety issues. The Contractor will respond to any reports referred by Lewisham, Police or other agencies within 24 hours, or as soon as reasonably practicable. The Contractor will maintain on site, a system for recording any incidents and any corrective action taken for inspection by Lewisham’s representatives. This will be forwarded to Lewisham on a regular basis. The Contractor will ensure as far as is reasonably practical, that necessary action has been taken and steps to avoid recurrence have been implemented.
- The Contractor will provide an information and reporting telephone ‘Hot Line’ staffed at all times during working hours. Information on this facility shall be prominently displayed on site hoardings. The Contractor’s nominated person will attend monthly reviews with Lewisham’s Environmental Protection Team, or otherwise as requested. The Contractor will facilitate Lewisham’s Environmental Protection Team to undertake regular planned inspections of the site to check compliance with the GPG and associated records.
- The Contractor will maintain regular liaison with the Horniman and the project team.
Training in relation to this plan
Contractors will abide by the Horniman’s ‘Rule for Visiting Contractors’.
The Contractor will provide training to all site operatives as part of their induction programme to ensure that the requirements set out in this plan are followed. They will also provide daily briefings and regular toolbox talks on specific topics.
The Contractor will ensure all site operatives hold the relevant CSCS card demonstrating proof of qualification and experience.
The Contractor will where necessary attend toolbox talks with specialist consultants (e.g. Ecology, UXO).
Appendix A
NLP-FF-00-XX-DR-A-00119 – Proposed Construction Management Site Plan FINAL
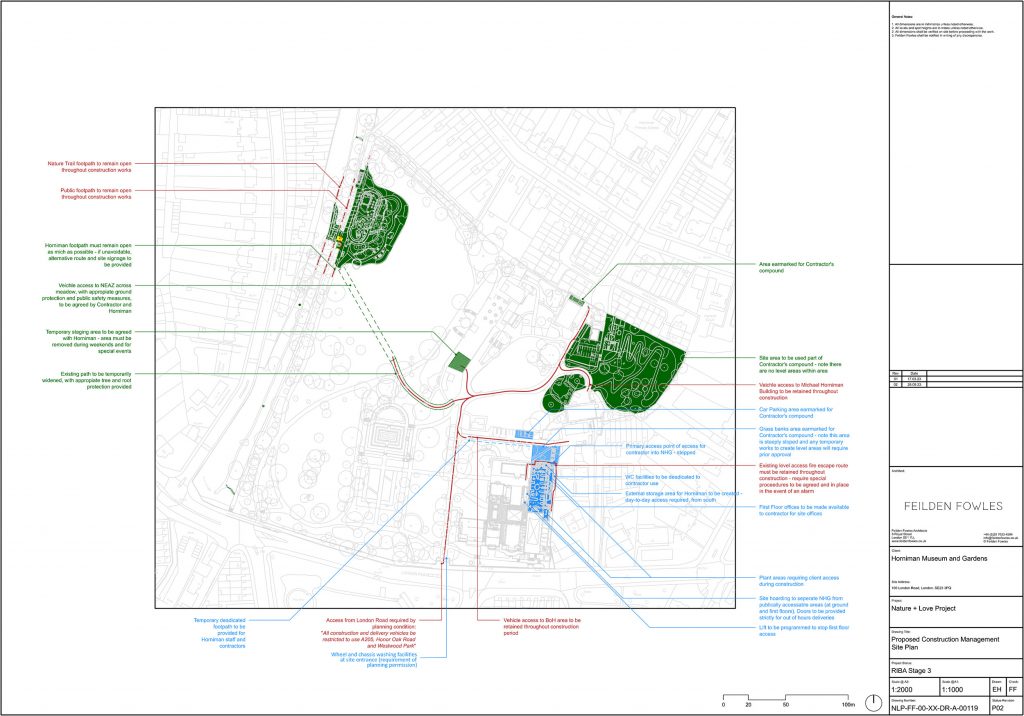
Appendix A – Gardens site map. For larger image, right click with your mouse and open image in new tab.
Appendix B
Download the Lewisham Good Practice Guide Control of Pollution and Noise from Demolition and Construction Sites.
Appendix C – Traffic Management Plan (Walter Lilly)
Traffic Management
Prior to commencement, a meeting will be held with the highways department of London Borough Lewisham to discuss and agree the proposed traffic management plan and logistic plan.
In preparing this section of the Traffic Management Plan (TMP) we have taken into consideration the following guidance
documents:
- London Borough of Lewisham Good Practice Guide
- TFL Construction Logistic Planning Guidance
- Construction Logistics and Community Safety (CLOCS) guidance
Prior to commencement of the works a meeting will be held with the Horniman Museum site management team to agree delivery arrangements. This is to ensure priory access is given to the Horniman Estate deliveries (estimate 10 per
day).
There will be careful planning and programming of deliveries and strict control will be enforced. 48 hours’ notice (two working days) must be give for deliveries and /or collections. Vehicles arriving out of sequence will be turned away.
Special loads may require several weeks’ notice pending Horniman Estate and Local Authority approval.
The contractor will endeavor to ensure that all heavy vehicle traffic is limited to times outside of rush hour, Monday to Friday. Construction vehicle movement will also be carefully planned and coordinated to avoid the AM and PM school drop off and collections. This will reduce congestion and safeguard pedestrians.
To ensure all contractors, delivery companies and visitors are aware of the traffic routes and restrictions, several methods will be implemented. This will include written briefings sent to delivery companies at the time of the orders being placed and verbal briefings within the site induction to all contractors and visitors to site.
Safety of cyclists is of paramount importance and all vehicles entering and exiting the site will fully comply with CLOCS, the requirement for vehicular safety equipment. Deliveries will abide by London standards recommended by the Construction Industry Cycling commissioning manifesto.
Traffic Marshal(s) will be provided to control site deliveries for both arrival and departure of all delivery vehicles. All delivery companies will be or encouraged to become members of FORS in accordance with the Tfl Construction Logistics Planning guidance for deliveries in London.
The Traffic Marshals will be fully qualified (Site Access Traffic Marshal qualification as a minimum) and will be always on duty during loading and off-loading activities to ensure that vehicles and pedestrians passing the site entrances do so in a safe manner.
All vehicles will enter the site in a forward direction and exit in a forward position. No reversing will be allowed onto the public highways. Vehicles will not be permitted to stack up. The construction vehicles will not block London Road or Horniman Drive.
Large deliveries and vehicles access will be made via the London Road gated entrance and access roads as shown on drawing NLP-FF-00-XX-DR-A-00119 shown above.
Smaller deliveries will be made via Horniman Drive entrance. All deliveries via Horniman Drive will be between 9-10am to avoid any disruption to residential areas.
At both London Road and Horniman entrances used by pedestrians there will be pedestrian management provided by the Traffic Marshals. All contractors site deliveries will be escorted through the site to ensure safe transit of the deliveries and a bankman will supervise any off-loading operations.
Indicative types of on-road vehicles arriving and departing the site are as follows:
- 9.11m (6) wheeled rigid “muck-away” lorry
- 6.65m (4) wheeled rigid small Flat bed with Hiab delivery lorry
- 5.2 m (4) wheeled general delivery van
- 8.73m (6) wheeled rigid ready mix concrete lorry
- 7.90m (4) wheeled skip lorry
See Indicative on-road vehicle data Appendix A.
All on road vehicles will comply with the Ultra Low Emission Zone (ULEZ) vehicle emission standards as a minimum. Evidence that contractors and suppliers have been contacted and their responses to the applicant in respect to the use of ULEZ compliant vehicle a ULEZ vehicle compliance form for the construction works will be issued to the London Borough of Lewisham Council monthly by e-mail. The use of Ultra-Low Emission Vehicles (ULEV) (e.g., Electric, Hybrid (Electric-Petrol) where possible will be encouraged at the procurement stage of the tender for these services.
The contractor will actively work with suppliers that can provide electric or hybrid vehicles. Subcontractors will be required to comply with the emission hierarchy where practicable. A software platform will be used to monitor the carbon footprint of deliveries, tracking the start, finish location and means of transportation. The ULEZ vehicle emissions compliance will be monitored monthly log sheet (See Appendix C).
All deliveries to site will be undertaken with full regard paid to:
- Reduction and control of plant movements
- All vehicles to be directed by a competent person
- Pedestrian and vehicle directional signage – suitable barriers will be erected to prevent pedestrian crossing the site entrances when deliveries are taking place.
- Mobile plant will only be operated by a competent person with a bank’s person in attendance to any movements.
Consultation with the local authority of the London Borough of Lewisham will continue throughout the project to
ensure:
- Construction methods minimise the potential impact on nearby residents. These include liaison with the residents on a regular basis and coordinate work to minimise disruption to residents, use of low emissions site plant equipment, limiting the amount of traffic movement to and from the site. Keeping dust and noise to a minimum by using noise and dust control measure (See AQDM plan).
- Maintenance of the existing public highway by using both London Road and Horniman Drive entrances. If one access route was to become blocked or unusable for third party reasons there is always a second access available.
- Segregation of all pedestrians, public or employees, on or in the vicinity of the site through the use of safe access routes and employment of Traffic Marshals.
Indicative Non-Road mobile machinery (NRMM) types for site use as follows:
- Telehandler-Material distribution
- Mini Excavator-Earthworks
- Dumper-Earthworks
- Spider crane-Lifting
See Indicative (NRMM) data Appendix B.
All non-road mobile machinery (NRMM) will comply with Stage IV Emission Standards (or the latest standard if the GLA requirements change) as a minimum if equal to or over 37kW. Where compliance with Stage IV requirements is not achievable or practical, an exemption will be sought from the GLA prior to arrival of the equipment on site.
The contractor will actively work with suppliers that can provide electric or hybrid vehicles. Subcontractors will be required to comply with the emission hierarchy where practicable.
The NRMM emissions compliance form will be monitored monthly (See Appendix D)
A – Indicative Plant Data sheets – Road Examples
Note: All suppliers will apply the emissions hierarchy relating to on-road Ultra Low Emissions Zone (ULEZ) compliant vehicles namely (1) Electric; (2) Hybrid (Electric-Petrol); (3) Petrol; (4) Hybrid; (Electric-Diesel) Diesel; (Euro 6 and Euro VI)
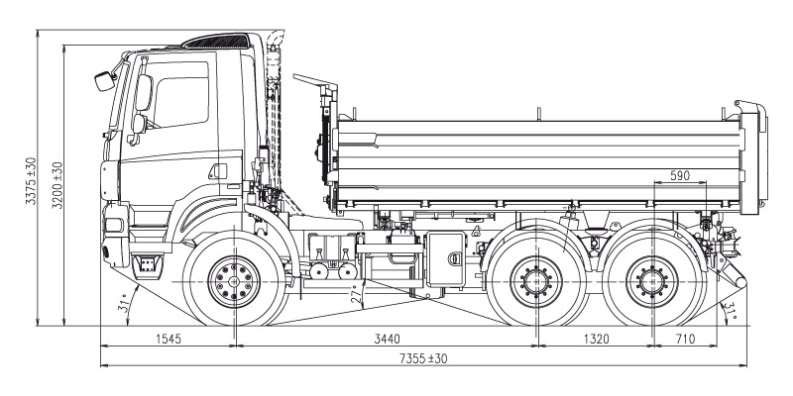
Example 1

Example 2
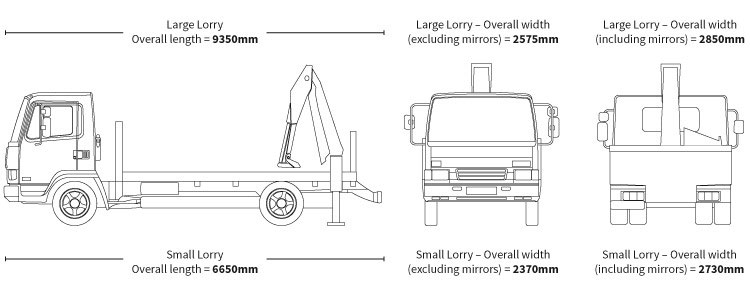
Example 3
B – Indicative Plant Data sheets-NRMM-Examples
Note: As Lewisham Good Practice Guide all non-road mobile machinery to use Ultra Low Sulphur diesel (ULSD).
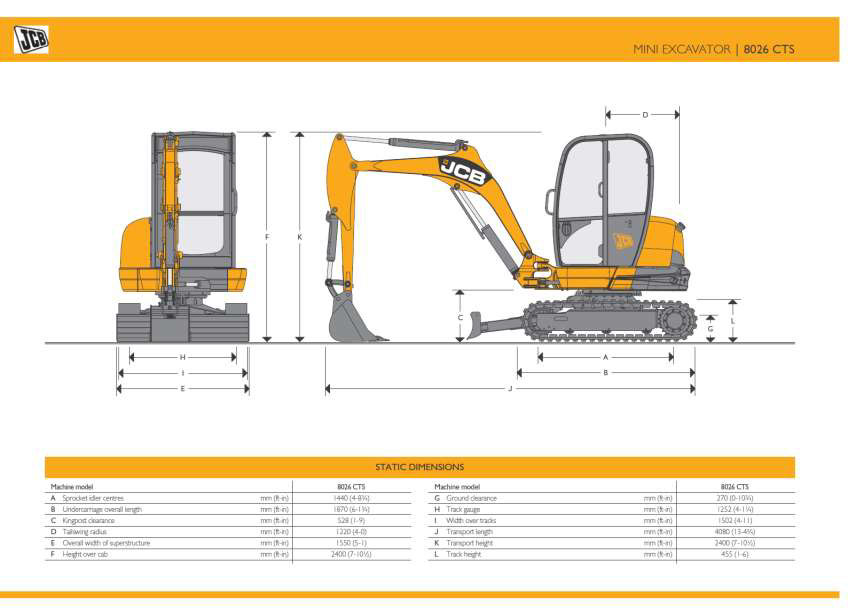
Example 1
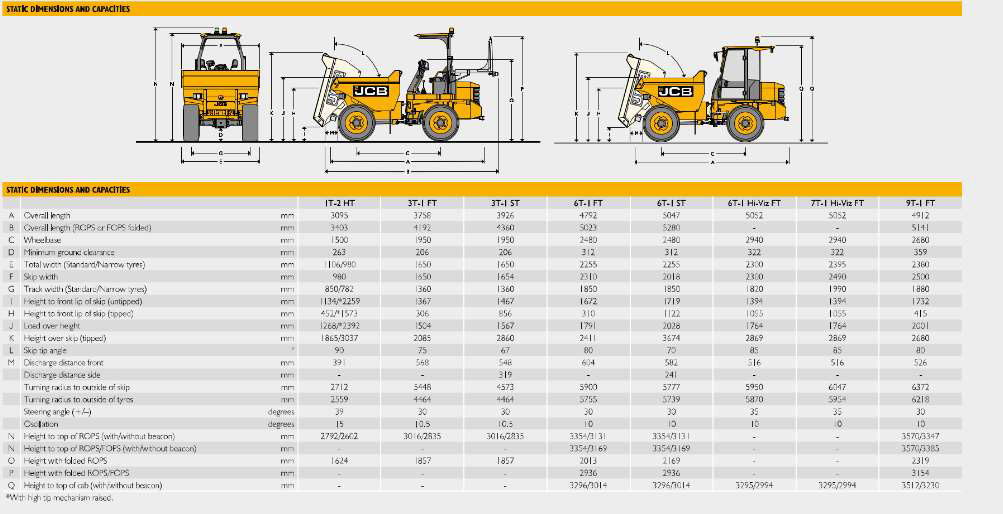
Example 2
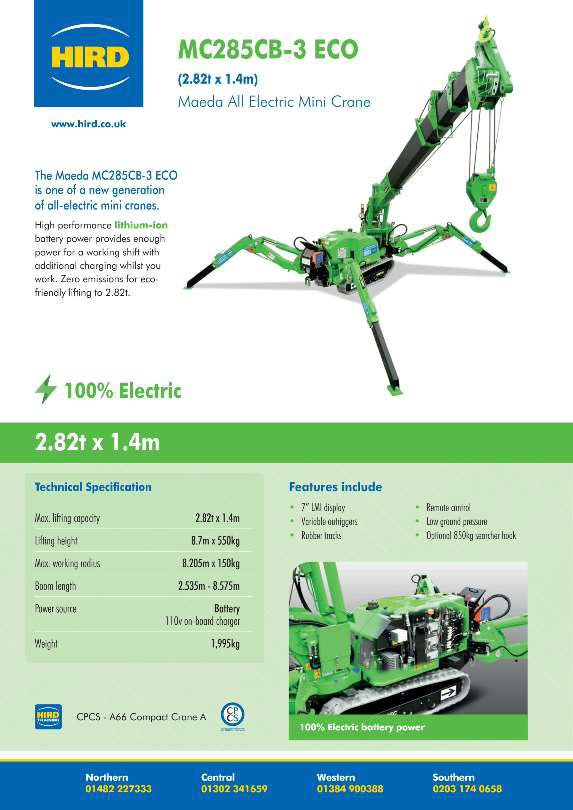
Example 3
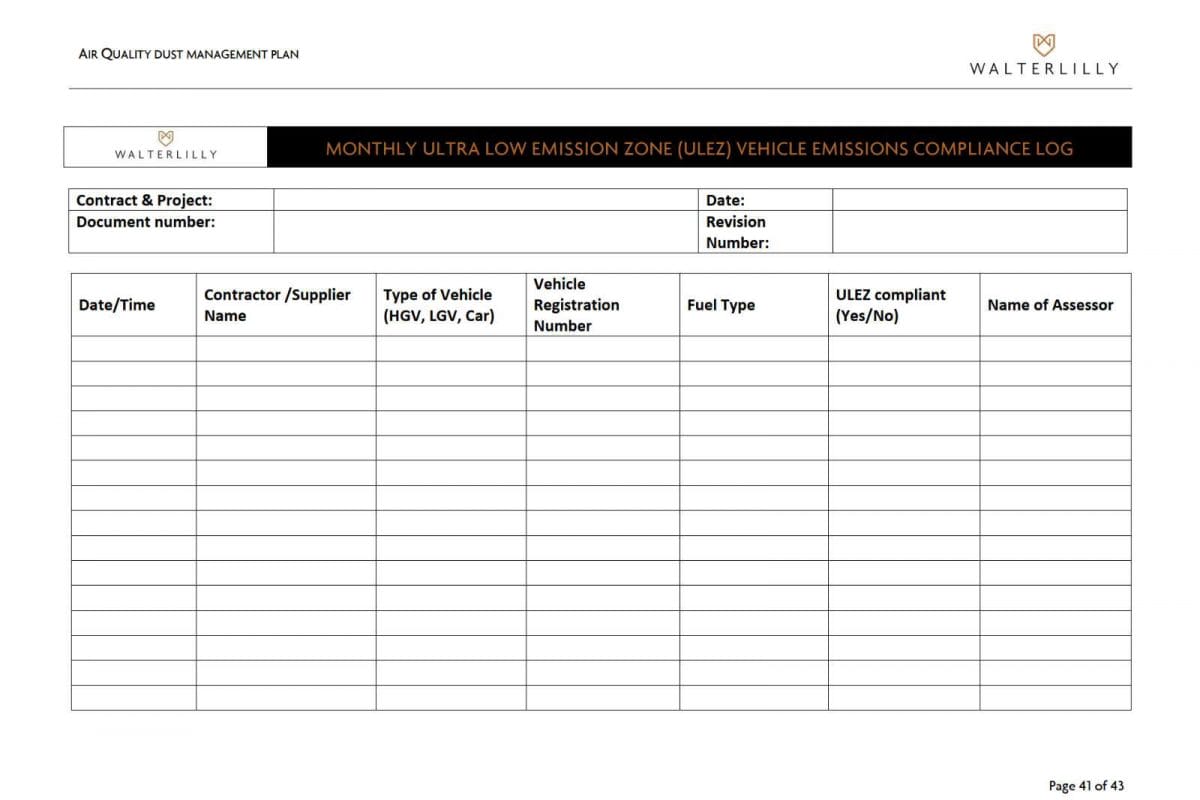
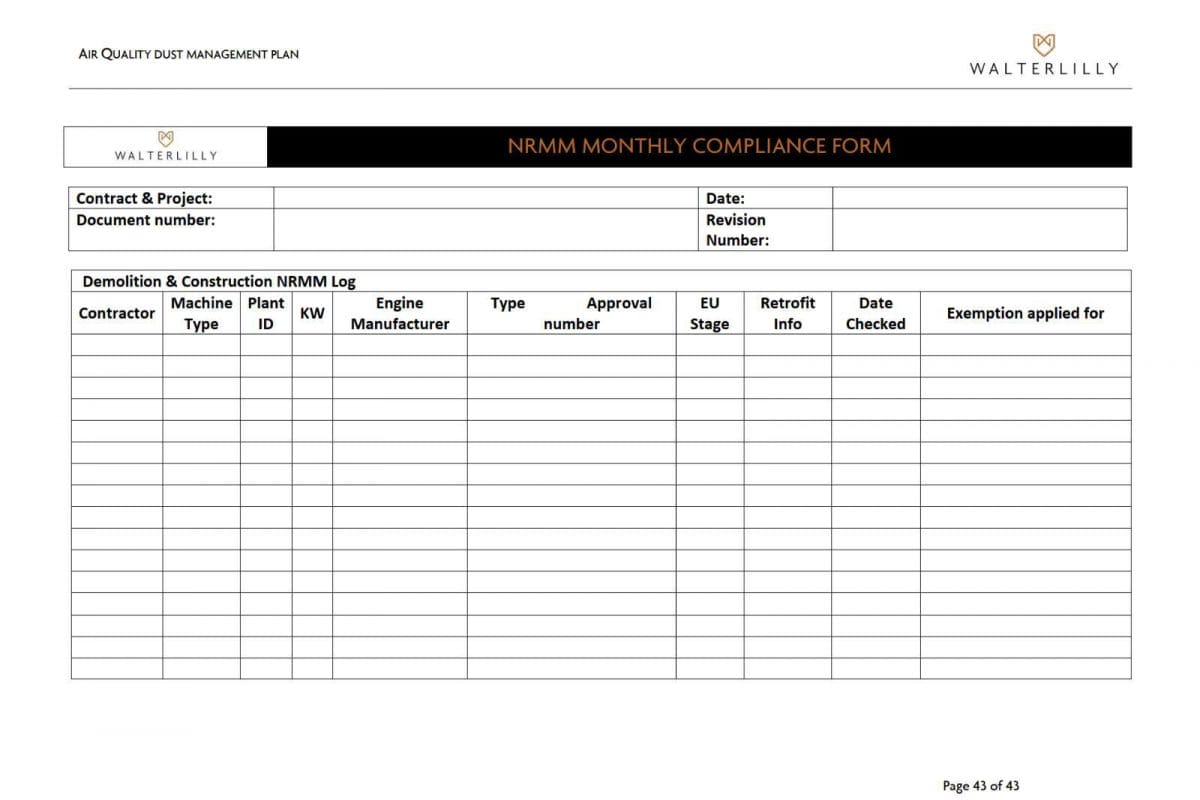
Appendix D – Dust Management Plan (Walter Lilly)
Air Quality Dust Management Plan
Air Quality Statement
The Horniman/Contractor is committed to applying the Air Quality Management standards required by Section 11 of the Planning Guidance Supplementary Planning document (London Borough of Lewisham) and confirm that we shall apply the relevant air quality control mitigation measures outlined in The Control of Dust and Emissions During Construction and Demolition Supplementary Planning Guidance document, produced by the Mayor of London and dated July 2014.
These are more fully described later in this Air Quality Dust Management Plan.
Introduction
Background
The purpose of the Air Quality Dust Management Plan (AQDMP) is to outline our approach to managing the construction impacts from dust and air pollutant emissions at the building project at the, in accordance with Planning Approval DC/23/130987 Condition 3 which states the following:
- Prior to the commencement of development hereby approved, a Dust Management Plan (DMP), based on an AQDRA (Air Quality and Dust Risk Assessment), shall be submitted to and approved, in writing, by the local planning authority. The DMP shall be in accordance with The Control of Dust and Emissions during Construction and Demolition SPG 2014. The DMP will need to detail the measures to reduce the impacts during the construction phase. The development shall be undertaken in accordance with the approved plan.
- Reason: To manage and prevent further deterioration of existing low-quality air across London in accordance with London Plan Policy SI 1 ‘Improving air quality’ and Policy T7 ‘Deliveries, servicing and construction’ of the London Plan (March 2021), and paragraph 181 of the NPPF.
- Approved details shall be fully implemented and permanently retained and maintained during the construction phases of the development. To comply with the requirements of the NPPF (2019), Policies 7.14a-c of the London Plan (2016) and policy CC10 of the Local Plan (2018)”
This document includes our Air Quality (Dust) Risk Assessment, inventory and timetable of dust generating activities, dust emission control methods to be employed, dust monitoring, Non-Road Mobile Machinery (NRMM), Ultra Low Emission Zone (ULEZ) vehicles, complaints and incident procedures.
During construction, site activities will have the potential to affect local air quality from dust deposition and increases in particulate matter concentration. Mitigation measures will be implemented to ensure that any impact on local air quality is minimised.
The agreed contents of this AQDMP will form part of the development plan, it is a Planning obligation requiring discharge by the London Borough of Lewisham (LBL) prior to commencement of work. The Plan will be regularly reviewed and any changes and/or improvements will be developed, added and agreed with the Council. The Plan will be revised and re-issued as necessary.
These proposals are to enable third parties to understand the nature of the works and the various construction activities associated with the development.
The AQDMP will be distributed to the Client and their consultant team and used for liaison with the stakeholders and other interested parties throughout the project. As information is updated and as the project develops, particular attention will be paid to the neighbours. This will ensure they are kept informed of progress and future works on the project. Communication will be via a monthly newsletter issued electronically and included in letter drops. (Amended from fortnightly Jan 2025).
The information provided in this document is an overview of the key project activities for the enabling and construction phase at Horniman Museum and Gardens Statements herein are to be further incorporated into plans, procedures and detailed method statements from newly appointed subcontractors as the project develops.
Project Overview
The Nature + Love project consists of a new Sustainable Gardening Zone, including demolition of existing structures and the construction of a new glass house with external covered area in the nursery hub, paved terrace, paths, and landscaping for the Winter Garden, paving and planting for Community Wellbeing Garden.
The construction of a new cafe, toilet block, store house and play area within old boating lake to Nature Explorers Zone, interpretation panels and entrance gate and ramp on the Nature Trail.
Internally to the Natural History Gallery the aim is to consolidate the showcase layout and reduce the overall number of showcases to improve the overall access routes and pinch points between the showcases. Many of the existing historic showcases are to remain and be refurbished, some will be repositioned and reallocated, removed or dismantled and placed in storage. A number of the existing more contemporary showcases are to be either relocated or removed. New display cases are to be installed to meet the modern criteria in terms of environmental conditioning.
External works to the Natural History Gallery to include new roof coverings, louvres to eastern windows; enlargement of western plant enclosure; plant enclosure on west side of gallery; ductwork penetrations, guardrails to east elevation, new fencing and gates and other internal and external alterations to the elevations at Horniman Museum and Gardens, 100 London Road SE23.
Guidance
This document has been prepared in accordance with the following guidance:
- Mayor of London SPG ‘The Control of Dust and Emissions during Construction and Demolition’, July 2014.
- Institute of Air Quality Management (IAQM). Guidance on the assessment of dust from demolition and construction, Version 1.1, June 2016.
- IAQM. Guidance on Monitoring in the Vicinity of Demolition and Construction Sites, October 2018.
- London Low Emission Construction Partnership (LLECP). Best in Class ‘Guidance on Dust and Emissions from Construction’ LLECP, March 2019.
- London Borough of Lewisham Good Practice Guide.
Project Overview
Site Description
The Horniman Museum and Gardens (the Site) is in Forest Hill, Southeast London, within LBL. The eastern boundary of the London Borough of Southwark is separated from the Nature Trail by the houses and gardens located on the eastern side of Wood Vale.
The Site first opened as Surrey House Museum in 1890 in the Horniman family residence. In 1901 it changed its name to the Horniman Museum when it re-opened in a new purpose-built museum building. The site was gifted to the people in 1901 for their education, recreation, and enjoyment. This vision remains central to the Horniman today.
The site consists of a mix of high-quality collections displayed in the galleries on site; these span natural, multicultural, and musical worlds alongside 16 acres of well managed open space. The Museum offers community based learning, education and leisure programs and a wide range of performance events and activities. The Horniman serves a local, national and international audience. It is a popular local resource in southeast London.
The Museum is Grade II* listed and has seen new extensions over the years including, most recently by Allies and Morrison in 2002. The Gardens are extensive and range in style and form from Sunken Gardens, Grasslands Garden, to the Sound Garden, Bee Garden, Wildlife Garden, Meadow Field, South Downs Meadow, and Prehistoric Garden. The Gardens underwent a significant redevelopment project in 2012 which provided new opportunities for education and creative pursuits.
The site is free to access and open to the public all year round. The Museum is open daily from 10am – 5:30pm and the Gardens open daily from dawn to dusk (time of year dependent).
Site Location Plan
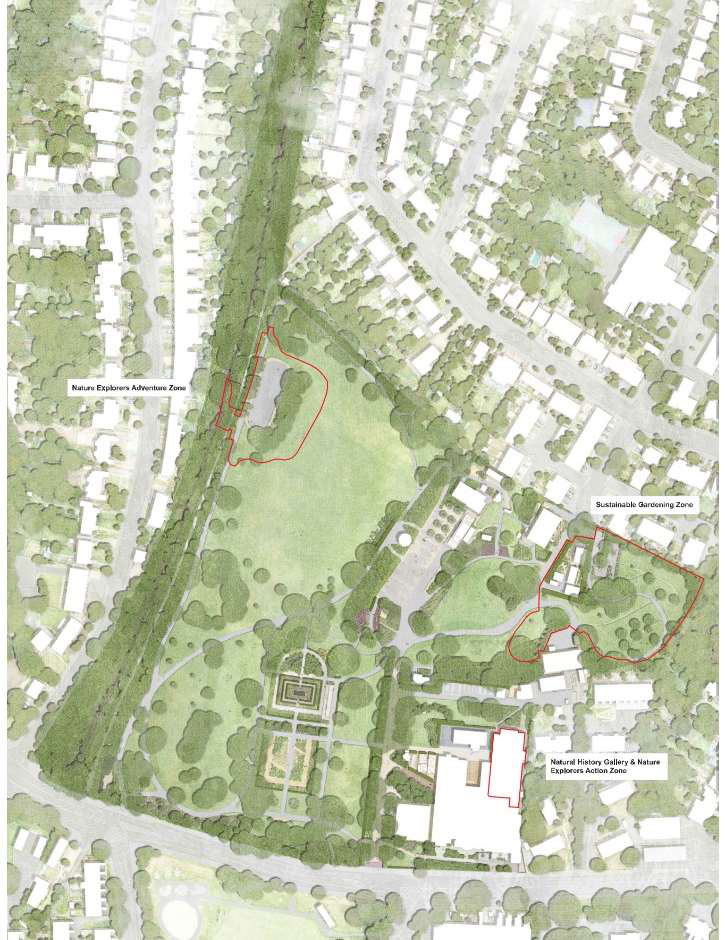
Site Location plan a
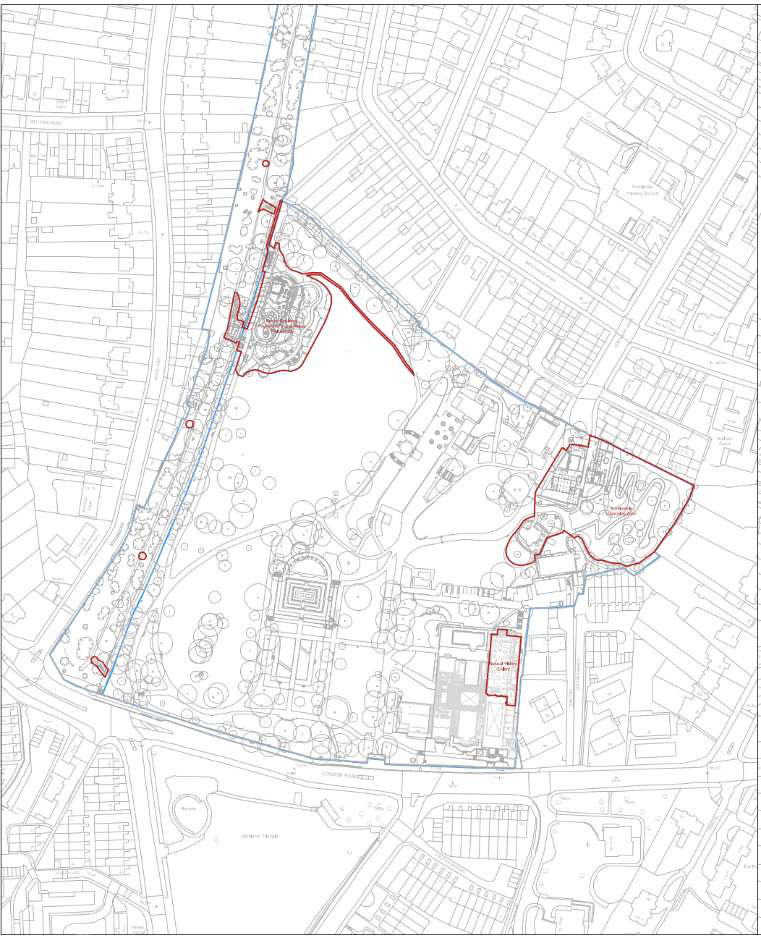
Site Location plan b
Proposed site works
Enabling works phase
The key elements of the enabling works development about the potential impact on the surrounding areas are:
- Secure site work areas using hoarding or Heras fencing panels.
- Set up contractors compound to include site office and welfare accommodation.
- Set up storage/staging areas.
- Form new vehicular and pedestrian access routes.
Note: – All the above as indicated on the proposed Construction Management Site Plan NLP-FF-00-XX-DR-A-00119- See section 3.2 below.
From site possession, an independent Environmental Consultant shall establish the noise, dust and vibration baseline monitoring levels.
Main construction works phase
The key element of the works with regards to the potential impact on the surrounding areas is: –
- Demolition works
- Substructure works
- Superstructure-Cafe
- Envelope-Roofworks
- External works-Sust
Roles and responsibilities
The appropriate resources will be supplied to cover the requirements of dust control on site to ensure that these are communicated effectively and acted upon in an appropriate manner. The site manager will be the person on site responsible for dust control and site activities in general. In the event of absence, responsibility will be assigned to another suitably qualified person.
Inventory and timetable of dust and NOx air pollutant generating activities
The following activities are identified as limited sources of dust emission to occur on this project (refer to works programme 023-0026 TMP1 in Appendix C & D Options).
- Demolition-Weeks 2-14
- Substructure-Excavation-Reduce Level Digs-Weeks 10-15
- Superstructure-Frames-Weeks 16-24
- Envelope & finishes-Weeks 14-30
See preliminary traffic movement plan below indicating maximum weekly traffic movements during the construction period. This histogram gives the indicative traffic movement based on 023-0026 TMP1 programme over approximately 71 weeks. The above is based on an average of 2 deliveries an hour on a “just in time” basis.
See Appendix C programme 023-0026 TMP-Maximum
The indicative traffic movements are based on the current allocated delivery slot of 9am to 10am (10 per week). Current restriction on traffic movement delivery times by LBL between 9-10 am to allow for school groups who may be travelling to and around site.
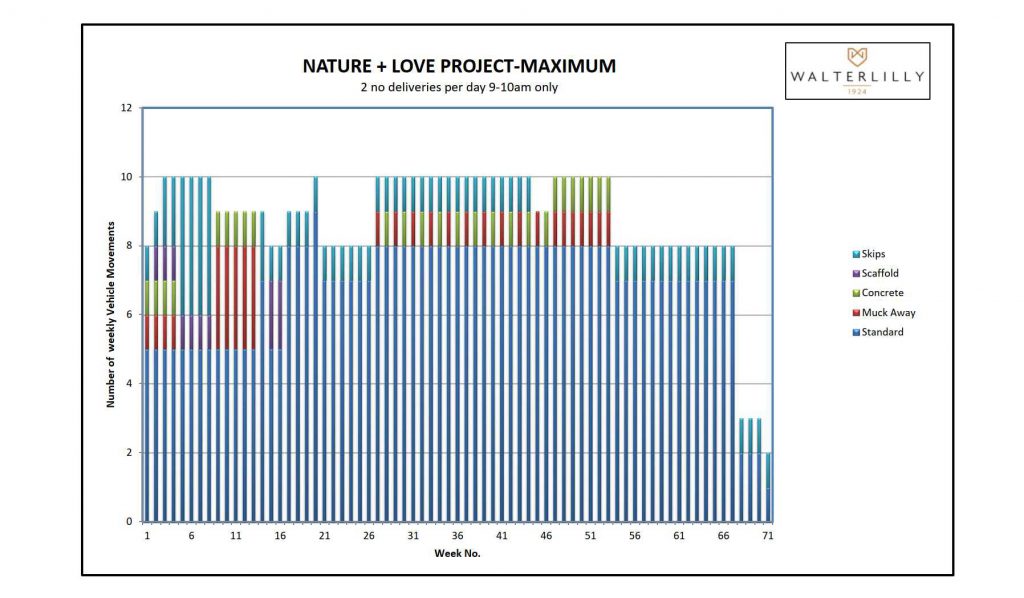
The maximum indicative traffic movement
The histogram below gives the optimum indicative traffic movement based on 023-0026 TMP1 programme over approximately 71 weeks. The above is based on an average of 2 deliveries an hour on a “just in time” basis.
This histogram shows the closest intent to the Focus high level delivery phase programme dated 21-07-23 and issued 13-10-23. See Appendix D programme 023-0026 TMP-optimum. Where traffic movements are likely to exceed the currently allocated slot of 9am to 10am (10 per week) this would require additional delivery slots between 6-7:30 am and 4-5:30pm between peak construction activity weeks 20-30 and weeks 43-48 reducing back down to the allocated slot weeks 49-63.
This would keep all deliveries clear of the local school run dropping-off and pick-up times.
This would give greater flexibility in achieving the optimum period on site for the construction works reducing the overall period down to approximately 8 weeks.
Note: Consideration can be given to earlier timed deliveries of prefabricated components to further reduce traffic
movements.
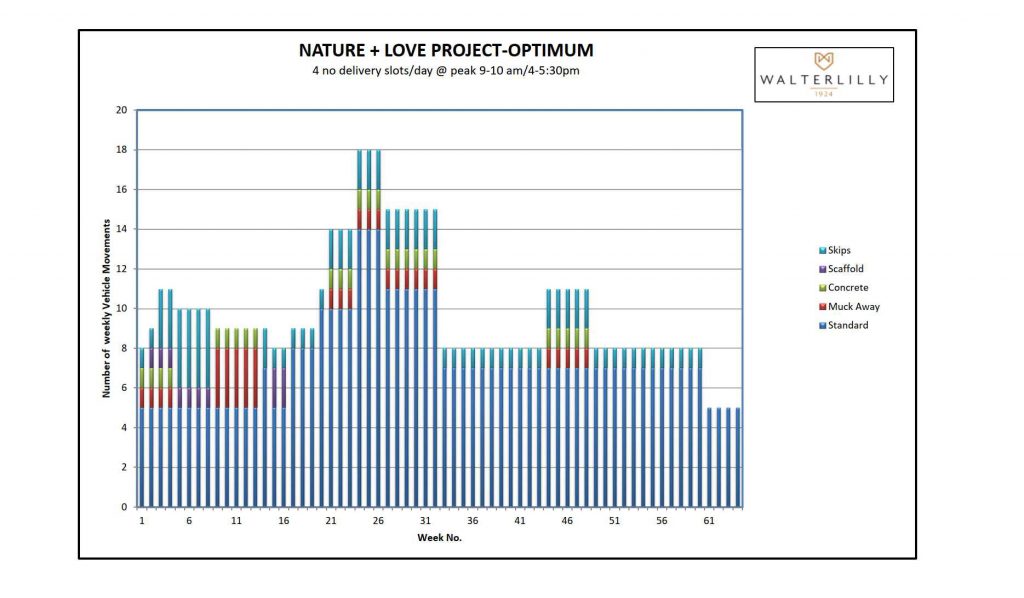
Four no delivery slots per day
COSHH
COSHH products will be stored in a locked container and items stored on bunds to ensure that they do not leak on to the surrounding area.
Spill kit and fire stations will be in the immediate vicinities to ensure, in the event of an accident, it can be dealt with quickly and efficiently. Spillages as covered in the Environmental Management Plan will be addressed in site inductions and toolbox talks so that all staff members are aware of how to manage should a spill occur on site.
Training
All site personnel will be made aware of the air quality issues covered in this plan during site induction.
- Regular Toolbox talks will be given to remind all site personnel of the requirements of dust management. Attendance records will be completed and filed appropriately to demonstrate good practice.
- All operatives will have a minimum of a CSCS card which includes environmental test questions as well as a site-specific induction which will set out the basic control measures of dust prevention.
- A training matrix will be completed, detailing the expected training requirements of individuals who have responsibilities on the project.
- Method statements and risk assessments will also be written (and briefed to all site personnel) before any works that may impact air quality are carried out on site. All subcontractors that are likely to undertake works with the potential for nuisance issues will read and sign to say they understand their Risk Assessment and Method Statement which will include the necessary environmental controls.
- Integrated into these documents will be the specific control and risk mitigation methods relating to the air quality issues detailed in this document.
Air Quality (Dust) Risk Assessment
The construction dust assessment considers the potential for impacts within 50m of the site boundary or within 50m of any road used by construction vehicles, up to 500m from the site boundary. The assessment methodology follows the Greater London Authority (GLA) Supplementary Planning Guidance (SPG) on the Control of Dust and Emissions During Construction and Demolition (2014) which is based on that provided by the Institute of Air Quality Management (IAQM). The Dust Emission Magnitude (DEM) is based on the scale of the anticipated works and the site will be classified as Small.
The risk evaluation considerations are based on the following steps:
- Step 1: Screen the need for a detailed assessment of human and ecological receptors.
- Step 2A: Define the potential dust emission magnitude based on the scale of anticipated works.
- Step 2B: Define the sensitivities of the area to any dust that may be raised.
- Step 2C: Define the risk of dust impacts without appropriate mitigation.
Walter Lilly’s site activities can be classified into four phases according to dust risk and are assessed based on site activities and the sensitivity of nearby receptors, these are: demolition, groundworks, construction and track out phases.
Step 1: Area sensitivity screening
The adjacent buildings and sensitive receptors to this site include:
- Horniman Museum campus including the Butterfly House
- Horniman Triangle playground
- Horniman Primary School
- Surrounding residential properties
Site Plan
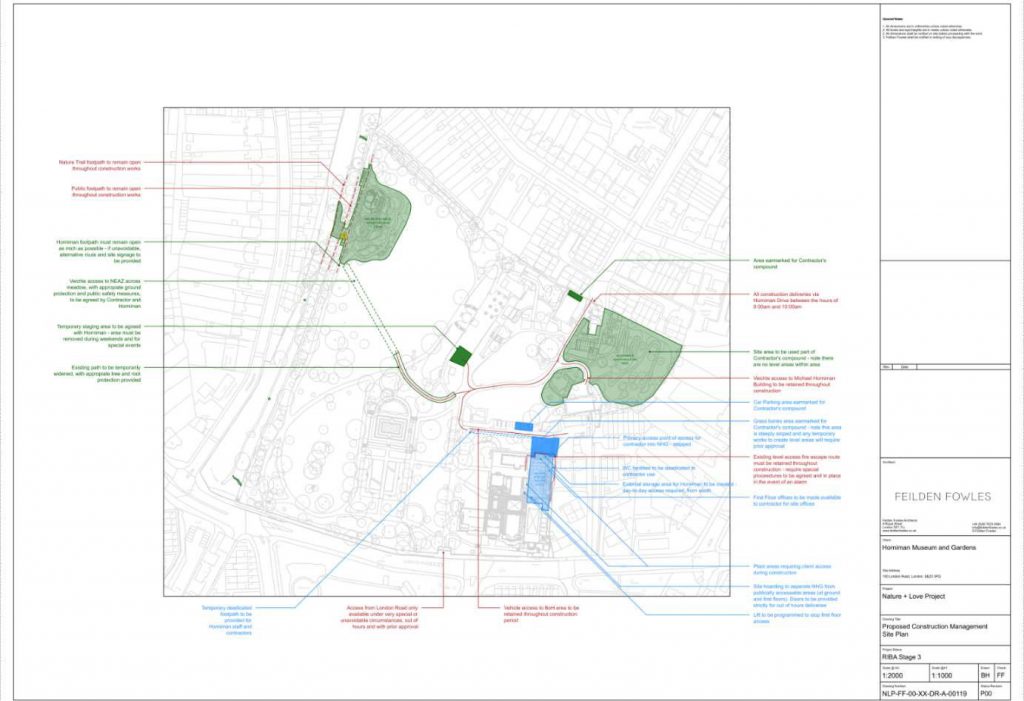
The site plan. For larger image, right click with your mouse and open image in new tab.
Step 2A: Dust Emission Magnitude
Demolition Phase
The phase of this project has been assessed as low risk based on the nature of the works involving dusty construction material (concrete). The extent of demolition (small quantity) falls into the category of small risk.
Earthworks Phase
Earthworks primarily cover excavation, haulage, tipping and stockpiling of soil type materials. This includes levelling the site excavating shallow raft foundations and landscaping.
The earthwork phase of the project is low risk based on the scope of works and the potential dust emissions during this phase.
Construction Phase
The key issues when determining the potential scale of dust emissions during the construction phase include the size of the building, the method of construction, the construction materials to be used and the duration of the build.
The scale of potential dust emissions from the site is low risk given the scope of prefabrication of the building components together with traditional methods in the construction phase.
Trackout Phase
Factors that determine the risk of dust emissions from the trackout are vehicle speed, geology and duration. Only receptors within 50m of the route(s) used by vehicles on the public highway and up to 500m from the site entrance are at risk from the effects of dust trackout.
The scale of potential dust emissions from the site is low risk. Dust emission magnitude overview:
- Demolition – Dust emission magnitude low
- Earthworks – Dust emission magnitude low
- Construction – Dust emission magnitude low
- Trackout – Dust emission magnitude low
Step 2B: Sensitivity of the area
The sensitivity of the area considers several factors including:
- The specific sensitivities of receptors in the area.
- The proximity and number of those receptors.
- In the case of PM10, the local background concentration; and
- Site specific factors.
The sensitivity of the area has been assessed for each phase of construction activity (i.e., demolition, earthworks, construction and track out) and the highest level of sensitivity has been addressed.
Sensitivity of people to dust soiling effects.
The sensitivity of people to dust soiling effects within the local area of this project has been assessed as medium based on the following principles:
- Users would expect to enjoy a reasonable level of amenity but would not reasonably expect to enjoy the same level of amenity as in their home.
- The people or property would not reasonably be expected to be present here continuously or regularly for extended periods as part of the normal use of the land (e.g., place of work).
Sensitivities of people to dust soiling effects:
- Receptor sensitivity: Medium
- Number of receptors: >1
- Distance from source:
- <20 – Medium
- <50 – Low
- <100 – Low
- <350 – Low
Sensitivities of people to the health effects of PM10
The sensitivities of people to the health effects of PM10 are based on whether receptors are likely to be exposed to elevated concentrations over a 24-hour period, consistent with Defra’s advice for local air quality management (Defra, 2009, LAQM Technical Guidance LAQM.TG (09)). This analysis to be carried out prior to the commencement of works.
The London Borough of Lewisham Air Quality Annual Status Report states the Annual Mean PM10 as 40ug/m3 (https://lewisham.gov.uk/myservices/environment/air-pollution/check-air-quality-levels.)
The sensitivities to health effects on this project have been assessed as low based on the following principles:
- Locations where members of the public are exposed over a time relevant to the air quality objective for PM10. In the case of the 24-hour objectives, a relevant location would be one where individuals may be exposed for eight hours or more in a day (e.g., Hospitals and schools)
Sensitivities of people to the health effects of PM10:
- Receptor Sensitivity – High
- Annual Mean PM10 Concentration – 40ug/m3
- Number of Receptors | Distance from the Source (m)e
- >100 | <20: high; <50: high; <100: medium; <200: low; <350: low.
- 10-100 | <20: high; <50: medium; <100: low; <200: low; <350: low.
- 1-10 | <20: high; <50: medium; <100: low; <200: low; <350: low.
Sensitivities of receptors to ecological effects
Dust can have two types of effects on vegetation: physical and chemical. Direct physical effects include reduced photosynthesis, respiration and transpiration through smothering. Chemical changes to watercourses or soils may lead to loss of plants or animals via changes in acidity. Indirect effects can include susceptibility to stressors such as pathogens and air pollution. These changes are likely to occur only because of long-term demolition and construction works adjacent to a sensitive habitat. Often impacts will be reversed when the works are completed
and dust emissions cease.
The sensitivities of receptors to ecological effects have been assessed as low based on the following:
- Locations with a local designation where features may be affected by dust deposition.
Sensitivities of receptors to ecological effects:
- Receptor Sensitivity: low
- Distance from the Source (m)c:
- <20 – low
- <50 – low
Additional factors to consider
The following additional factors have been considered when determining the sensitivity of the area:
- Any history of dust generating activities in the area.
- The likelihood of concurrent dust generating activities on nearby sites.
- Any pre-existing screening between the source and receptors.
- Any conclusions drawn from analysing local meteorological data which accurately represent the area;
and if relevant.
- The season during which the work will take place.
- Any conclusions drawn from local topography.
- Duration of the potential impact, as a receptor, may become more sensitive over time; and
- Any known specific receptor sensitivities which go beyond the classification given.
Step 2C: Risk of dust impacts with no mitigation applied
The below tables combine the dust emission magnitude determined above with the sensitivity of the area determining the risk of impacts with no mitigation applied.
It is Walter Lilly intention to apply maximum mitigation measures more than the requirement to better ensure that a non-nuisance environment exists for all receptors.
London Borough of Lewisham on the Annual Mean is 40ug/m3.
Risk of dust impacts – Demolition:

Risk of dust impacts – demolition
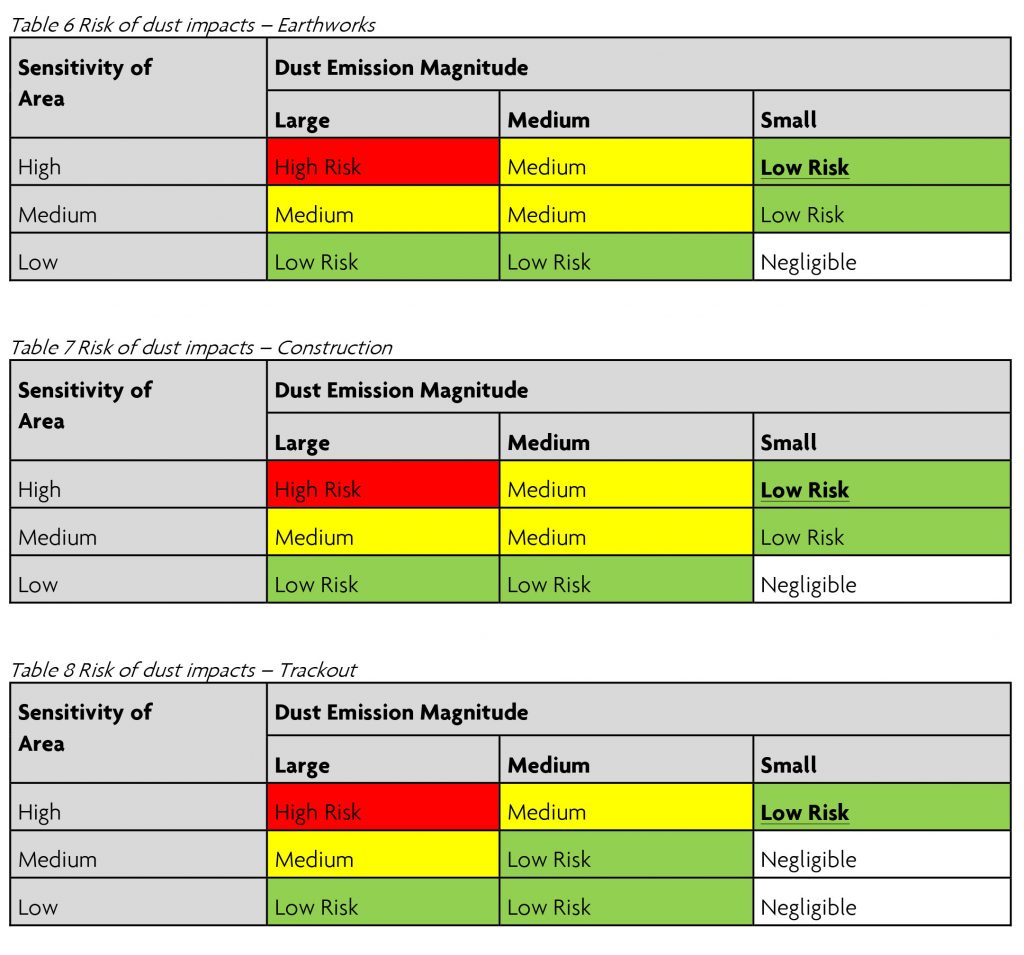
Risk for dust impacts – earthworks, construction and trackout
Dust and Emission Control Measures
The overall dust risk classification of the site is low in accordance with the Mayor of London SPG ‘The Control of Dust and Emissions during Construction and Demolition July 2014 Measures to mitigate dust emissions will be required during the project period on Horniman Museum and Gardens to reduce health related dust nuisance for all local receptors.
Referring to visible dust, it is imperative to prevent statutory nuisance arising from the demolition, construction works or dusty activities. Therefore, a philosophy of prevention of dust formation in the first instance shall be adopted. Dust management should be addressed through 1. Prevention, 2. Suppression and 3. Containment.
These three principles are well established and are central to the control strategies to control dust. They follow a hierarchy to control the emissions.
The Mayor’s SPG on The Control of Dust and Emission During Construction and Demolition outlines the best practice measure that should be adopted, where appropriate, to reduce the impact of a medium risk site, along with guidance on the monitoring that should be undertaken throughout the project period. This reflects best practice experience and will be applied, together with the experience and input of the professional consultant and the findings of the dust impact assessment.
The measures outline mitigation procedures of a low-risk site which we will implement on site to minimise dust nuisance from our operations. Included are correct storage of raw materials, high standards of housekeeping and site management, minimisation of drop heights and consideration of the prevailing wind.
Suppression techniques will be using water via hoses and dampening down of localised areas during dusty activities during the demolition / construction phases. We will ensure that we have an adequate supply of water on site that has adequate frost protection.
Regardless of regular inspections and procedures, should any airborne dust be seen to be leaving the site boundary the source of the emission will be immediately identified and corrective action will be taken without delay.
These measures are outlined below in section 4.1.
Regardless of the risk level, Walter Lilly will ensure that our employees and subcontractors on site always follow best practice to control and limit dust and emissions into the atmosphere from the minor demolition and construction activities, including vehicles and plant. Regular inspections will be made throughout the project in adherence with Walter Lilly’s ISO14001 Environmental Management System. All qualifying plant will be registered on the NRMM register and regularly monitored to ensure compliance.
We understand the importance of management techniques for effective control of dust and emissions, our techniques include:
- Proper management, supervision and training for process operations.
- Proper use of equipment (e.g., misting cannons).
- Effective preventative maintenance on all plant and equipment concerned with the control of emissions to air;
and
- In addition to the above, effective preventative maintenance will be employed throughout all phases of the site activities including all plant, vehicles, buildings and the equipment concerned with the control of dust and emissions to air.
Construction mitigation measures
The below points outline Walter Lilly’s proposed mitigation measures which will be implemented throughout the project for low-risk site following review above:
Mitigation measure in line with Mayor of London (SPG July 2014)
Implemented on site = XX – required / X – desired
Site Management
- The name and contact details of the individual accountable for air quality emissions and dust generated from the site displayed on the site boundary, along with the head or regional office contact information – XX
- A site log recording complaints and outcomes of the site inspections in the forms in (Appendix A and B will be issued to the council by email upon request) – XX
- Record any complaints and exceptional incidents that cause dust and air quality pollutant emissions, either on-site or off-site, and the action taken to resolve the situation in the site logbook – XX
Preparing and maintaining the site
- The site logistic plan developed so that Stockpiles, NRMM plant and dust-causing activities are located as remote as possible from off-site residential receptors – XX
- Site runoff of water or mud excluded – XX
- Site fencing, barriers and scaffolding kept clean using wet methods – XX
- Waste Materials removed from the site a minimum of three times a week – XX
- Stockpiles covered or fenced to prevent wind whipping – XX
- The use of localized hoarding and Heras fencing will be provided in key areas – XX
- Solid screens or barriers erected around dust activities or the site boundary that are, at least, as high as any stockpiles on site – XX
- Site or specific operations will be fully enclosed where there is a high potential for dust production and the site is active for an extensive period – XX
Operating vehicle/machinery and sustainable travel
- Use contractors and suppliers that can provide non-diesel, hybrid, and electric vehicles where possible at the procurement stage of the tender for these services – X
- All non-road mobile machinery (NRMM) for engines of 37kW-560kW will comply with the minimum Stage IV emission standards set in EU Directive 97/68/EC and its subsequent amendments unless the machinery is not available or that a comprehensive retrofit to meet both PM and NOx emission standards is not feasible – XX
- Avoid idling – All on-road vehicles will have their engines switched off when stationary – X
- The existing site mains electricity power supply where possible to be used. The use of nondiesel, hybrid, or electric vehicles to be encouraged – X
- Secure tool storage on site to avoid the need for contractors to travel by van every day – X
- The Construction Logistics Plan (CLP) adhered to minimize the impact of on-road demolition vehicle emissions and restrict on-road demolition vehicle trips to off peak hours – XX
- A Travel Plan developed that supports and encourages sustainable travel e.g., public transport, cycling, walking – X
Operations
- Cutting, grinding, or sawing equipment used where fitted or in conjunction with suitable dust suppression techniques such as water sprays or local extraction, e.g., suitable local exhaust ventilation systems – XX
- An adequate water supply on the site for effective dust/particulate matter suppression/mitigation using non-potable water where possible and appropriate. Handheld sprays used. In addition, high volume water suppression systems, manually controlled, can produce fine water droplets that effectively bring the dust particles to the ground – X
- Enclosed chutes, conveyors and covered skips used – XX
- Drop heights from loading shovels, hoppers and other loading or handling equipment will be minimized, and fine water sprays will be used on such equipment wherever appropriate – XX
- Equipment will be readily available on site to clean any dry spillages, and clean up spillages as soon as reasonably practicable after the event using wet cleaning methods – XX
- The project team will use public transport to travel from the office to the site where possible – X
Waste Management
- Waste recycled where possible to reduce dust from waste materials – XX
- Waste Materials removed from the site on average 2/3 times per week – X
- Bonfires and burning of waste materials not permitted – XX
Measures Specific to Demolition
- A soft strip inside buildings before demolition (retaining walls and windows in the rest of the building to provide screening against dust – XX
- Water used during demolition operations. Handheld sprays used for water. Water droplets that effectively bring the dust particles to the ground – XX
- No explosive blasting or mass demolition. Manual and or mechanical alternative methods will only be used – XX
- Any biological debris bagged and removed or damped down before demolition – XX
Measures Specific to Earthworks
- Earthworks and exposed areas/soil stockpiles covered or fenced to prevent wind whipping and will be re-vegetated to stabilize surfaces, as soon as practicable – XX
- Secure covers removed in small areas during work and not all at once – XX
Measures Specific to Construction
- Sand and other aggregates will be stored in bunded areas and will not be allowed to dry out, unless this is required for a particular process, in which case appropriate additional control measures will be put in place – XX
- Only small supplies of fine powder materials will be used on site, and bags will be sealed after use and stored appropriately to prevent dust – XX
- Scabbling (roughening of concrete surfaces) will be avoided if possible – XX
- Water-assisted dust sweeper(s) used on the access and local roads, to remove, any material tracked out of the site daily if required – XX
- Vehicles entering and leaving the site covered to prevent escape of materials and dust during transport – XX
Measures Specific to Track out
- Vehicles leaving the site inspected and cleaned to ensure that any mud or other dust causing materials from the vehicles prior to exiting onto the highway – XX
- A maximum speed limit of 5mph on surfaced and un-surfaced on-site haul routes and work areas within the site signposted – XX
- A wheel washing system with rumble grids to dislodge accumulated dust and mud prior to leaving the site to be installed at the site entrances off London Road and Horniman Drive as the proposed Construction Management Plan NLP-FF-00-XX-DR-A-00119 – See 3.2 Site Plan section
above – XX
Dust Monitoring
Following the dust risk assessment above of the site the project is considered a low-risk category. In line with the Mayor of London “the control of dust and emissions During Construction and Demolition Supplementary Guidance (July 2014)” dust monitoring equipment is not required for this low-risk site.
The residual impact of air quality and dust on occupational exposure will be considered to minimise workers exposure and any breaches of air quality objectives that may occur outside the boundary. This will take the form of regular visual assessments and logged on the Dust Monitoring Report (Appendix A).
An accurate log of complaints from the public with be kept on site recording the measures taken to address complaints where they are required. There will be ongoing communication with the main contractor and the Horniman Estates Team regarding any comments from the public.
Meteorology
The risk of dust impacts is highly dependent on meteorological conditions. High wind speeds increase the potential for dust to be raised and blown from the site while dry periods reduce the particle cohesion and therefore increase the potential for dust generation. High risk weather conditions include:
- Wind speeds greater than 5.0 m/s; and
- Prolonged periods of dry weather.
The wind speed and direction will be measured on site and monitored by the Site Manager to alert staff to potential adverse conditions that may trigger the additional mitigation measures outlined in Section 4.
Visual Assessment
The frequency of visual inspections will be increased when activities with a high potential to produce dust are being carried out on site such as during demolition and earthworks. The frequency of inspections should also be increased during periods of adverse weather, i.e., during periods of dry weather with high wind speeds.
Regular off-site inspections will consist of a walk around the perimeter of site and making observations about dust emissions and dust soiling, particularly focusing on locations upwind of onsite activities. Observations will include regular dust soiling checks of surfaces such as street furniture, cars and window cills in close proximity to the site boundary, with cleaning to be provided if necessary. Inspection results will be recorded in a Dust Monitoring Form (See Appendix A) and any specific notes relating to dust soiling or dust generating activities will be noted.
These Dust Monitoring Forms can be issued to London Borough of Lewisham Council as and when requested.
Complaints and incident procedures
It is the responsibility of the Site Manager to record, respond to and follow up all complaints regarding dust. Site Managers are responsible for ensuring that suitably qualified personnel are available to always respond to complaints.
Actions to be taken by the Site Manager:
- Note the time, date, name and contact details of the complainant. Note if the complaint has been referred from the local authority. Ask complainant to describe the dust emission or nuisance; is it constant or intermittent, how long has it been going on for, is it worse at any time of day/any day of the week, does it come from an identifiable source.
- Within a day after receipt of a complaint undertake a site inspection. Note all dust producing activities taking place. If the complaint was related to an event in the recent past, note any dust producing activities that were underway at that time, if possible. Implement any remedial action as necessary.
- Within a day after receipt of a complaint, visit the area from where the complaint originated to carry out a visual inspection and ascertain if dust is still a problem.
- If another source of dust other than the construction work is identified as causing the nuisance, verify the source. Photograph the source and emissions.
- Within a week after the initial investigations have been completed contact the complainant to explain any problems found and remedial actions taken.
- If necessary, update any relevant mitigation measures to prevent any recurrence of problems.
- Ensure that the Project Director is notified that a complaint has been received, what the findings of the investigation were, and any remedial measures taken. This should be done within two weeks of a complaint being received; and
- Inform workers on site of any complaints, the findings of any investigations and what remedial measures should be taken.
Dust Soiling Monitoring
If complaints are received regarding dust soiling close to the development site, then a period of dust soiling monitoring may be undertaken to determine whether the dust affecting the complainants is likely to be generated by the site, and whether the level of dust soiling experienced has the potential to be considered a nuisance.
Dust soiling monitoring should be undertaken for a minimum period of 4-6 weeks but may be continued for longer periods if high levels of dust soiling are measured. Dust soiling monitoring would involve the deployment of monitors such as sticky pad or glass slide dust gauges at several locations including at affected receptors and at the boundary of the site closest to these properties, as well as at background locations upwind of dust generating activities.
Any dust soiling monitoring regime would be discussed and agreed with London Borough of Lewisham Council prior to commencement. Where any high levels of dust soiling are identified which may be caused by demolition and construction activities at the development site, additional dust mitigation measures will be implemented. Further monitoring may then be undertaken to demonstrate the effectiveness of such mitigation measures.
On-Road Vehicle and Non-Road Mobile Machinery (NRMM) Emissions
On-Road Vehicles
The use of Ultra-Low Emission Vehicles (ULEV) (e.g., Electric, Hybrid (Electric-Petrol) where possible will be encouraged at the procurement stage of the tender for these services.
The contractor will actively work with suppliers that can provide electric or hybrid vehicles. Subcontractors will be
required to comply with the emission hierarchy where practicable.
NRMM
Non-road mobile machinery (NRMM) is defined as any mobile machine or vehicle that is not solely intended to carry passengers / goods on the road. The emissions requirements are only applicable to diesel (including diesel hybrids) powered machines / vehicles.
All non-road mobile machinery (NRMM) will comply with Stage IV Emission Standards (or the latest standard if the GLA requirements change) as a minimum if equal to or over 37kW. Where compliance with Stage IV requirements is not achievable or practical, an exemption will be sought from the GLA prior to arrival of the equipment on site.
Use of NRMM will be minimised as much as possible and electric or battery powered alternatives will be used as a preference. If NRMM under 37kW is to be used, use of the equipment will be minimised and kept as far away from sensitive receptors as is practicable. For NRMM under 37kW, the contractor will endeavour to use equipment fitted with after treatment devices where practicable.
NRMM where the power output is less than 37kW will be fitted with an after-treatment device (DPF) stated on the approved list managed by the Energy Saving Trust; the ongoing conformity of plant retrofitted with suitable after treatment devices, to a defined performance standard, should be ensured through a programme of onsite checks.
The project team will cooperate with local authority inspections and provide the requisite information as required.
Approved details shall be fully implemented and permanently retained and maintained during the demolition and construction phases of the development.
Appendix B – NRMM Monthly Compliance Form
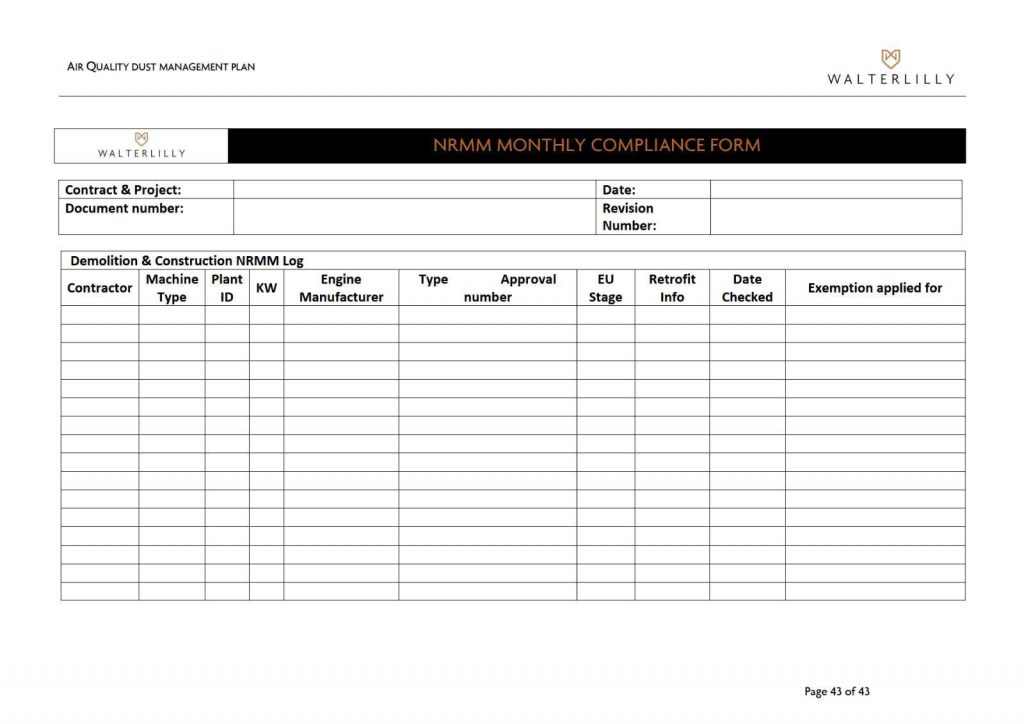
Example of NRMM monthly monitoring form
Appendix C – Programme Option 1 Histogram Data Maximum Intent
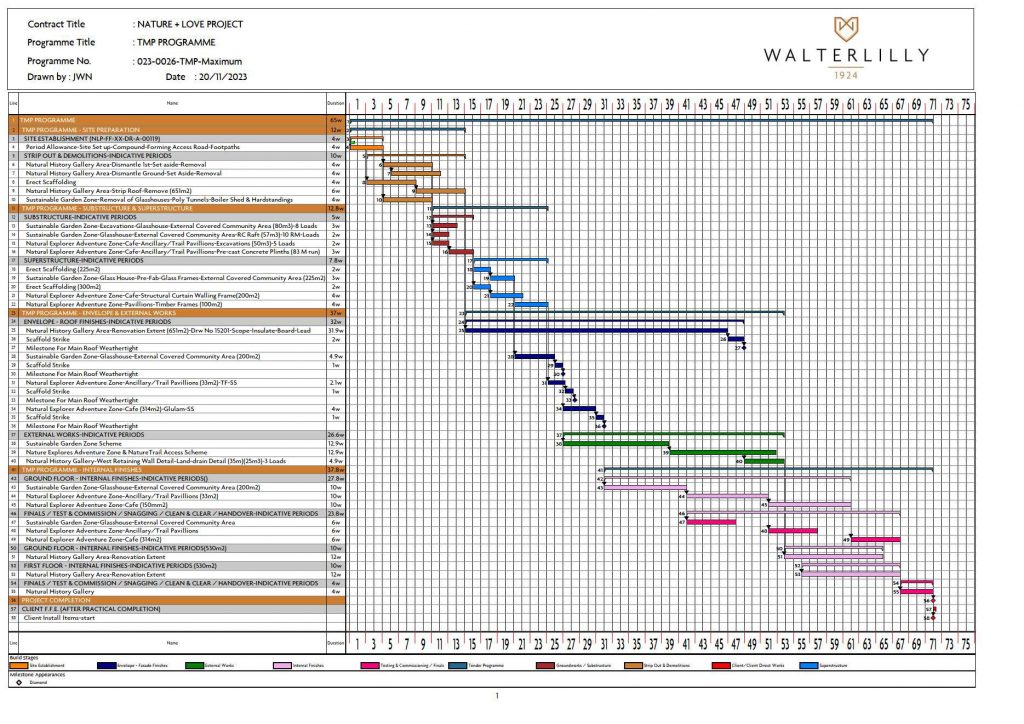
Maximum
Appendix D – Programme Option 2 Histogram Data Optimum Intent
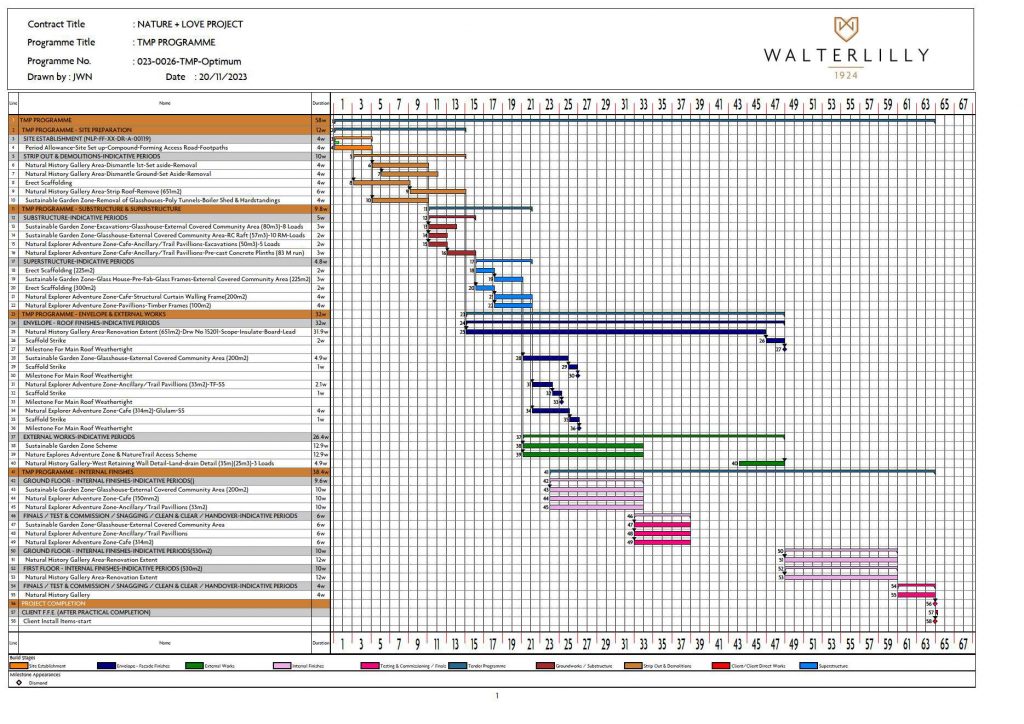
Optimum intent
Download the page as PDFs, including the two new appendices – C and D:
Getting in touch
If you are a local resident and have questions about the works, please do get in touch with us via framework@horniman.ac.uk